Ahh, the level 3 sentry gun. The holy grail of Team Fortress 2 props. It only took me about a decade to get around to....
Immediately after finishing the "level 1" sentry gun (I use "level one loosely as I look back on it somewhat unsatisfied with the proportions and scale, but more on that in another post) I went to work on the level three, which looks like this:
Immediately after finishing the "level 1" sentry gun (I use "level one loosely as I look back on it somewhat unsatisfied with the proportions and scale, but more on that in another post) I went to work on the level three, which looks like this:
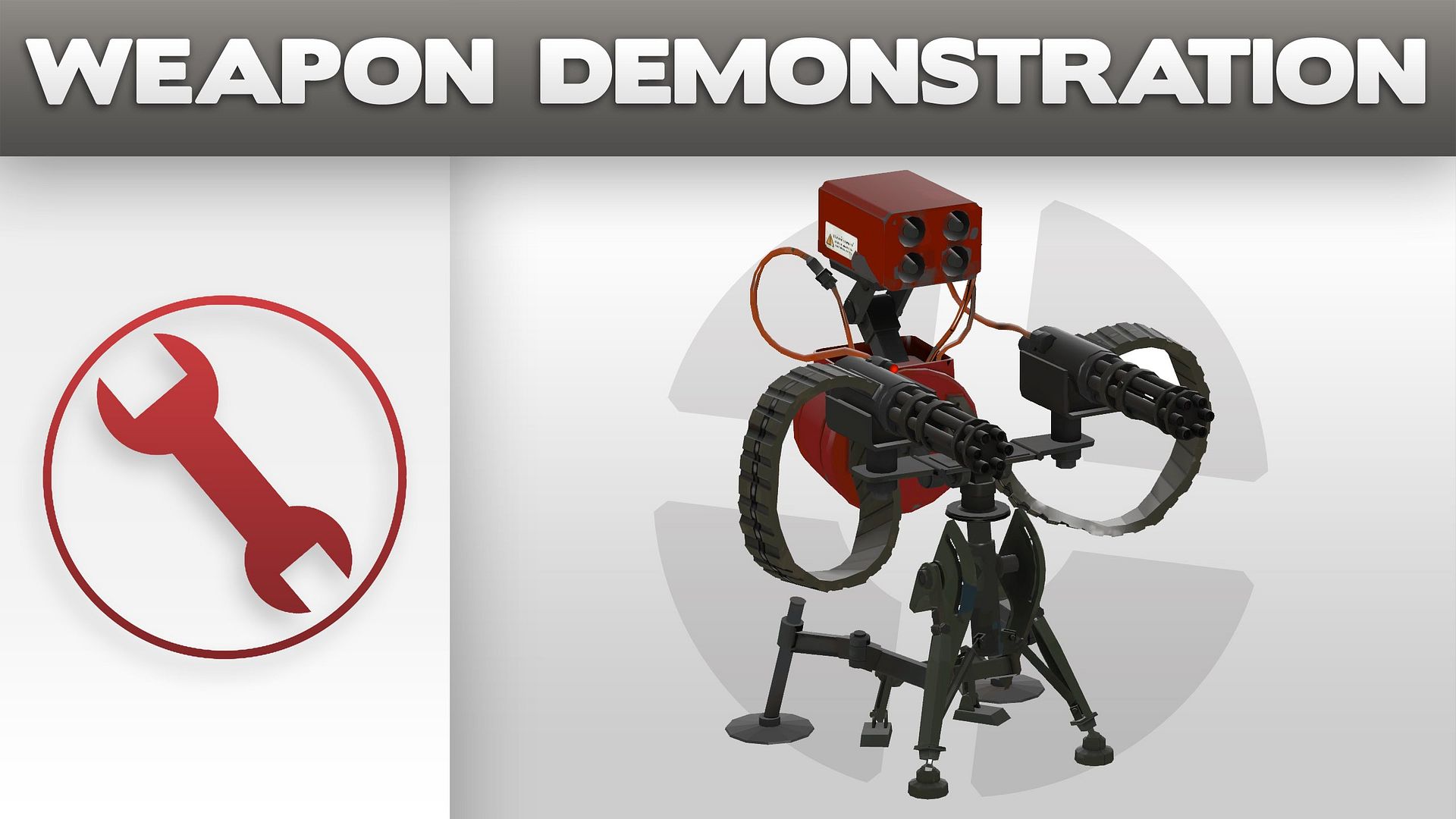
I paid slightly more attention to scale and proportions, but like my first version, ultimately didn't make any blueprints or anything. I just eyeballed it from a few screen shots.
I also didn't think 8 years ago people would be reading my blogs, so my photos are horrid on this project and are taken with a flip phone in a messy garage and/or bedroom up until a certain point. This sentry gun survived (Mostly) 5 moving trips during my time in college and right after. I refused to let it go, and was adamant about finishing it one day. When I say I'm going to do something, I do it. It might take me 8 years, but I do it dammit!
21 year old me started on the base, using the same materials and techniques as the previous sentry.
I made the miniguns out of an MDF frame with lots of supports, and a thin wrap of styrene for the skin. Then the well for the ammo belt feed and other details and layering were made. I skimped on photos here. That, or they got lost long ago.
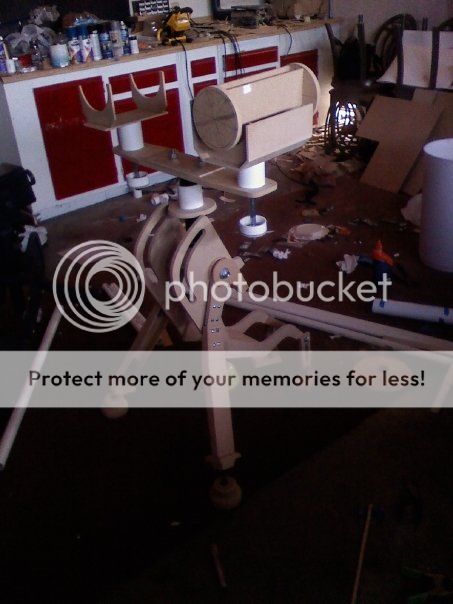
It started looking imposing at this point, especially at low angles. TMI.
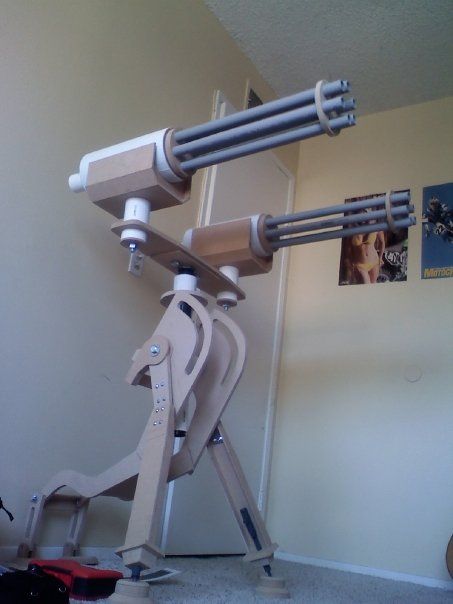
Like the previous build, the canister was made out of a polypropylene trash can. Glue and paint doesn't stick to it particularly well, so it needed a lot of sanding and reinforcements to bite the paint and glue.
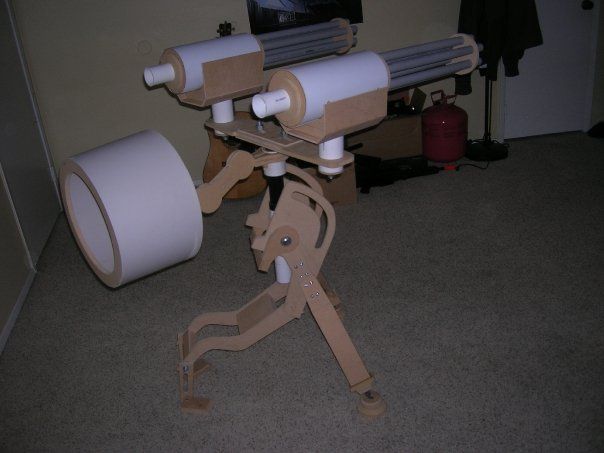
The missile pod was made from sheet styrene, as well as the support arms and shroud around the canister. This all had to be as light as humanly possible as the design is not only back heavy, but that little support arm is made from MDF... not the strongest stuff in the world. Not to mention it would later be supporting thick cables, a few layers of sealing and paint, plus the giant ammo belts that plug into the back end. The "holes" for the missiles are solo cups. I wasn't exactly the worlds wealthiest 21 year old, and this whole project only cost me around 100-200 bucks in the end in raw materials. That's about $2.08 in sentry gun monthly payments over 8 years. I can live with that. People do dumber things with their coin....
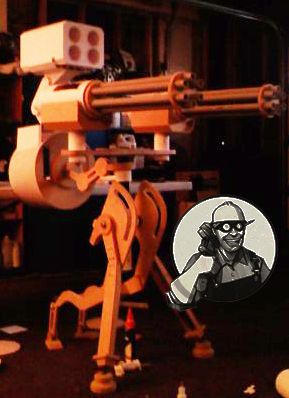
Getting a little bit ahead of myself, I began to seal and paint everything. Which, could have been worse since it sat like this for years.
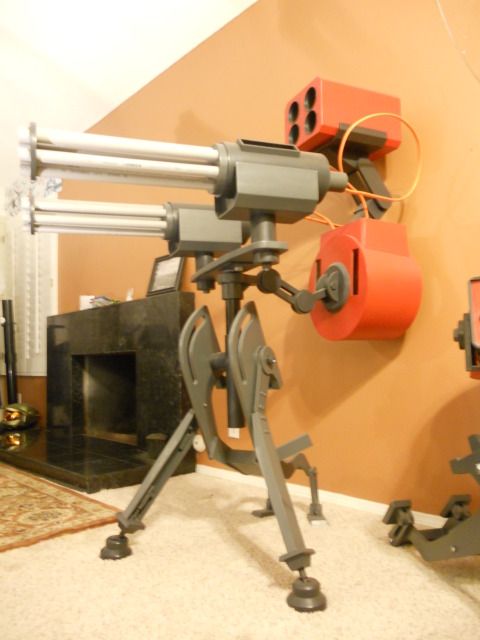
Then after school I found myself on the move quite a bit. During one of the last moves, I left the miniguns in my hatchback during the summer. They baked in the car and were in direct sunlight for at least a day. Styrene as you might know is a thermoplastic, and warps considerably in high temperatures. One of the skins on the cannons became warped to high heaven. the other less so, but noticeable still. I ripped the un-salvageable one apart.
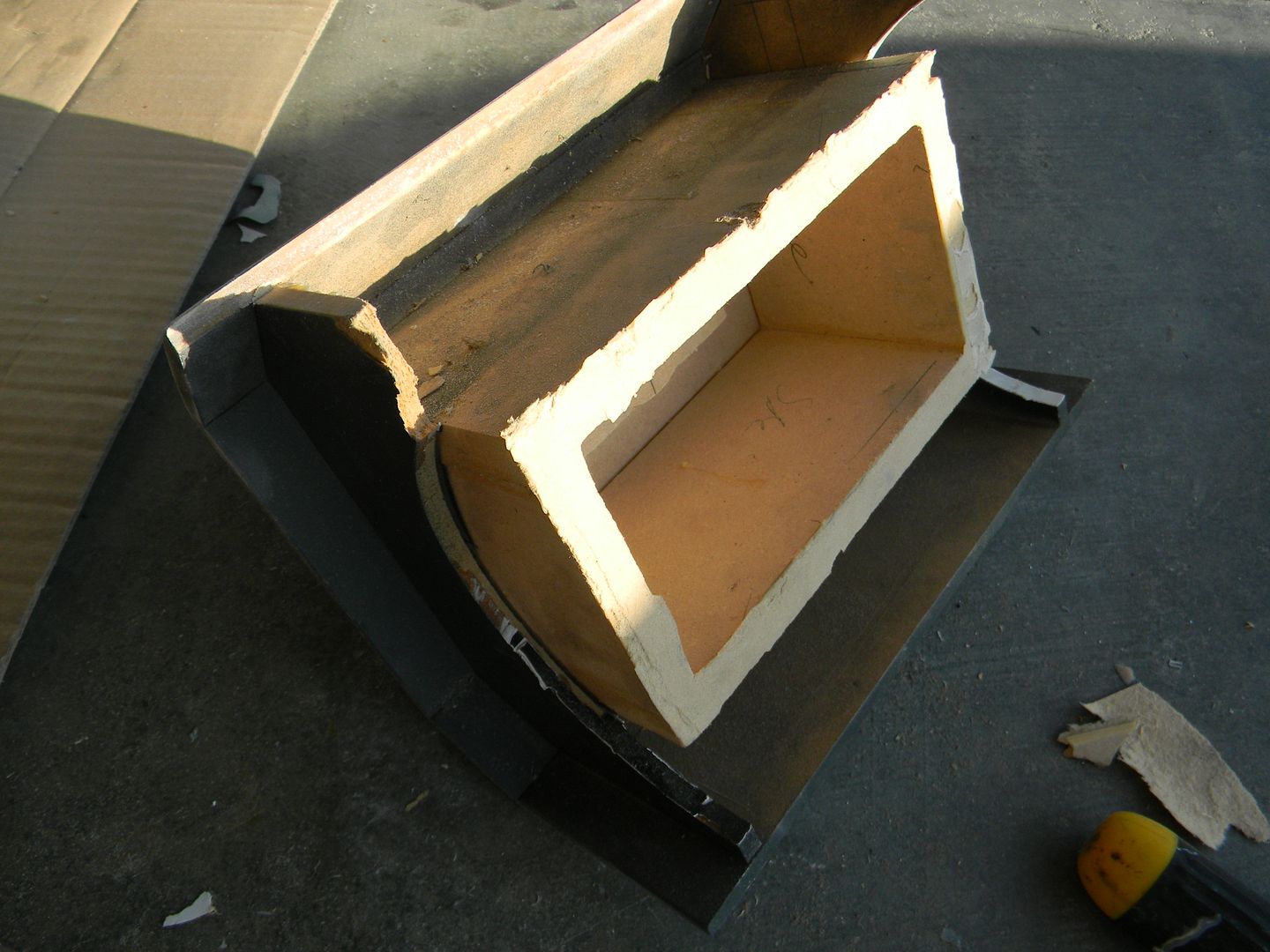
I had forgotten how tough I made these. It didn't just de-laminate at the frame like I was hoping. The parts supporting the styrene were everywhere, and as a result everything broke to some degree when taking it off.
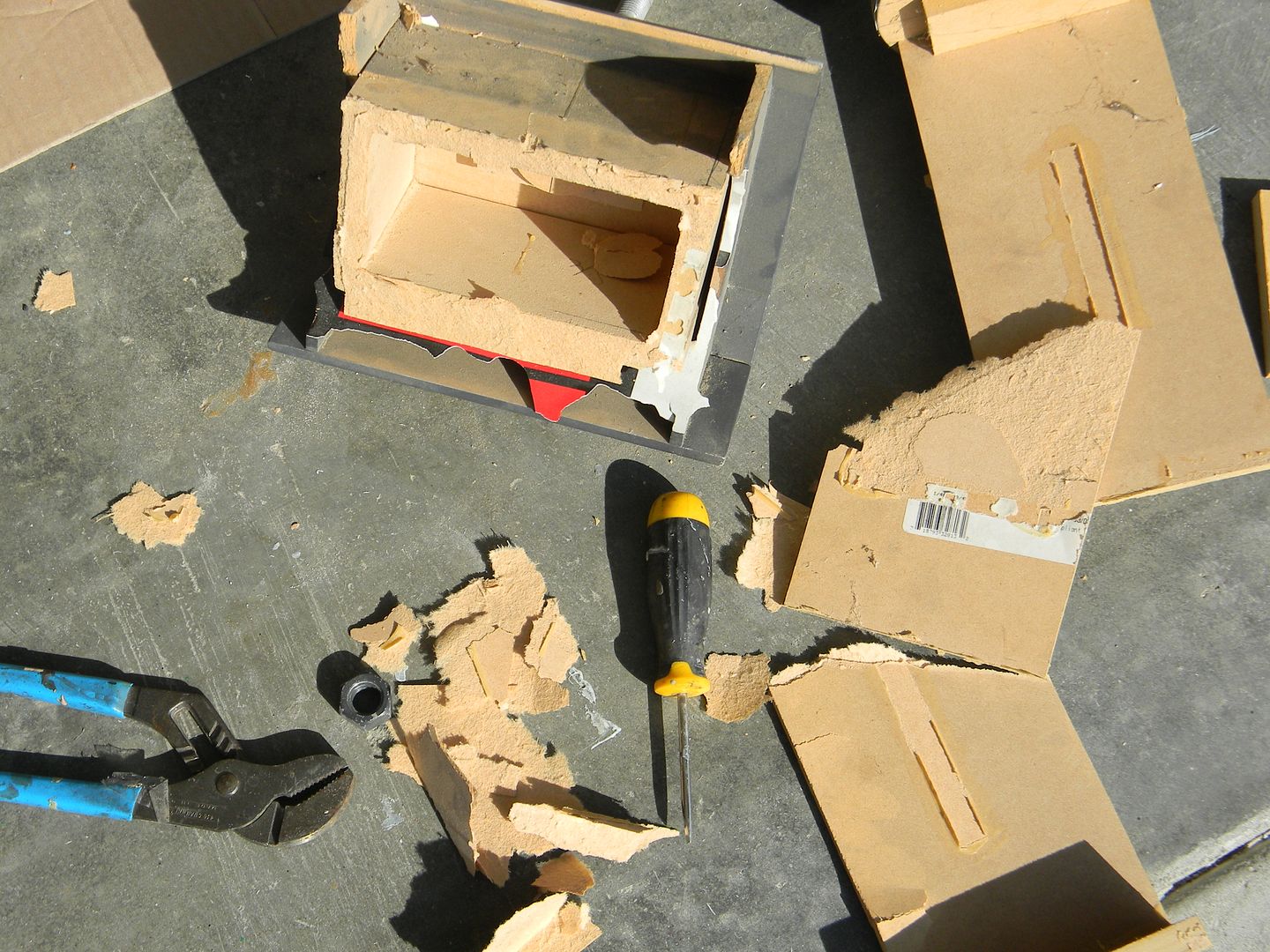
Even though it wasn't as bad as it looks, it still took me half a day to salvage what I could without remaking the whole thing, which I was quite happy with considering if one of those supports was off or the circles weren't concentric, the whole thing would wrap together nicely and be structurally or cosmetically sound enough.
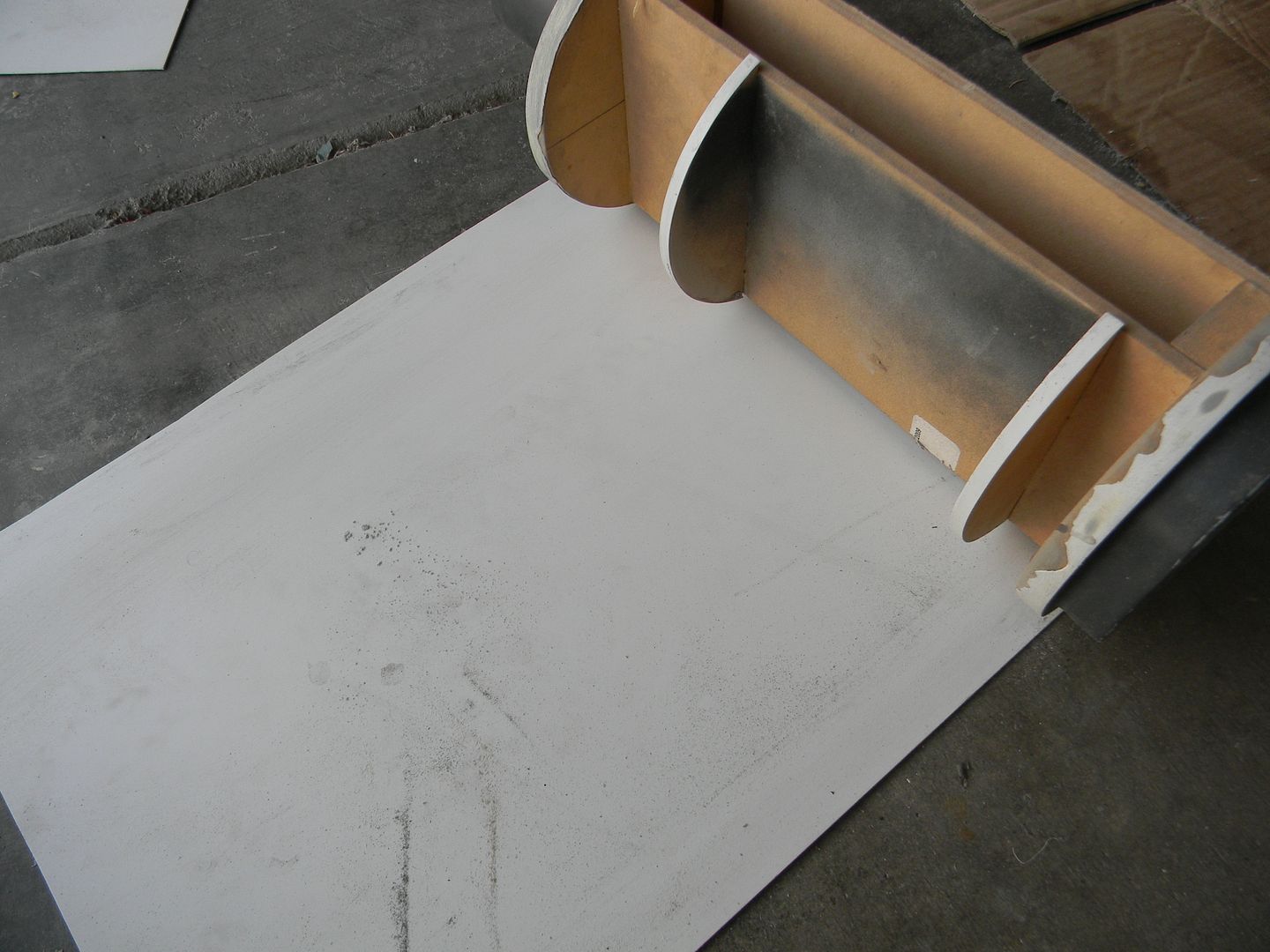
I used thicker styrene this time, so the heat wouldn't distort it. At least in my state's temperature range. A bit more fussy to do, but worth the peace of mind. I taped it in place and let the glue dry.
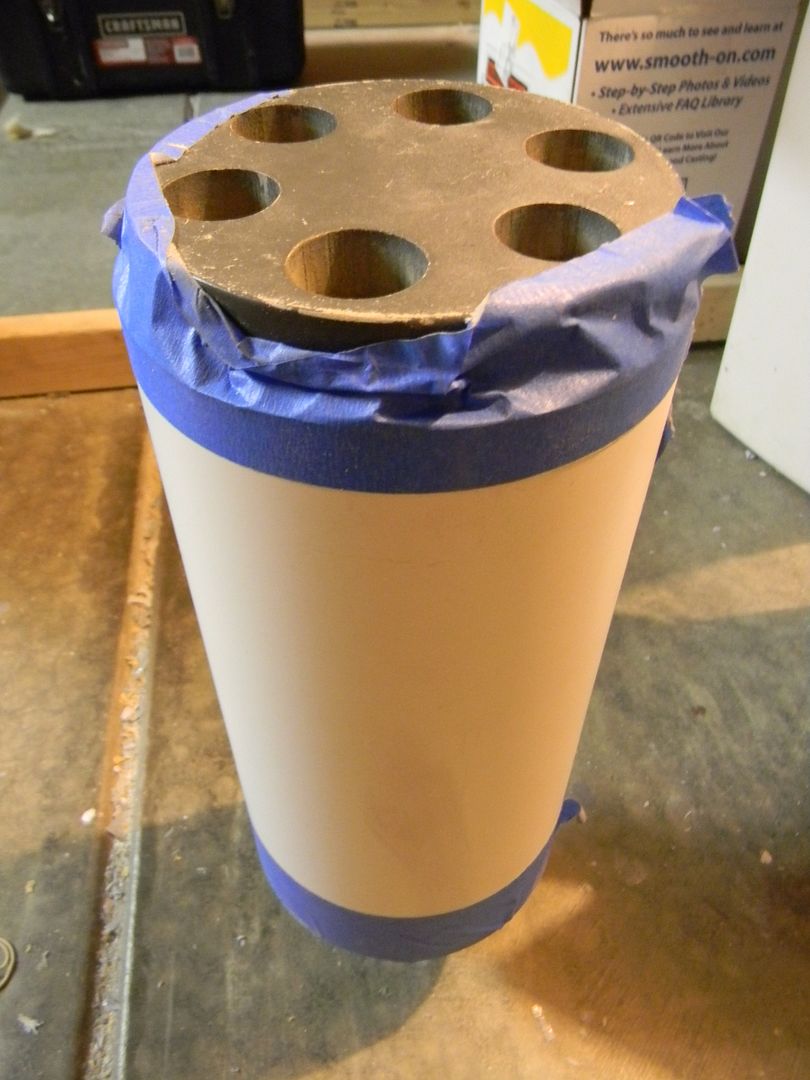
I cut the hole for the frame mount. Its harder than it looks, because if the hole is too small, it obviously won't sit. If the hole is too big, or crooked, a gap might show and there is no way to patch it and still preserve the curvature that is supposed to be there. I simply marked and measured, using masking tape edges as guides. Great success. Is nice.
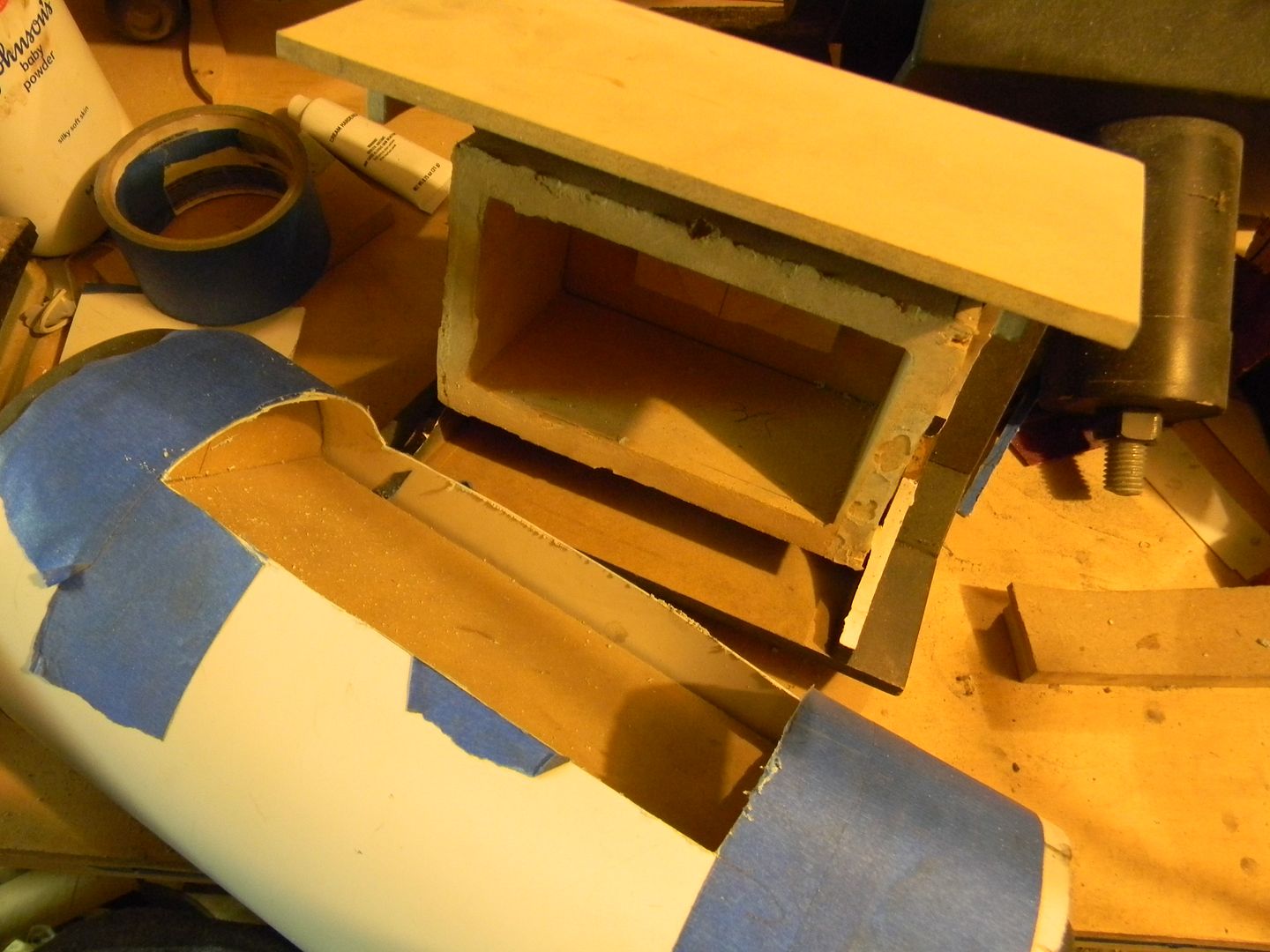
I caked on some wood glue and hopefully it will last many years.
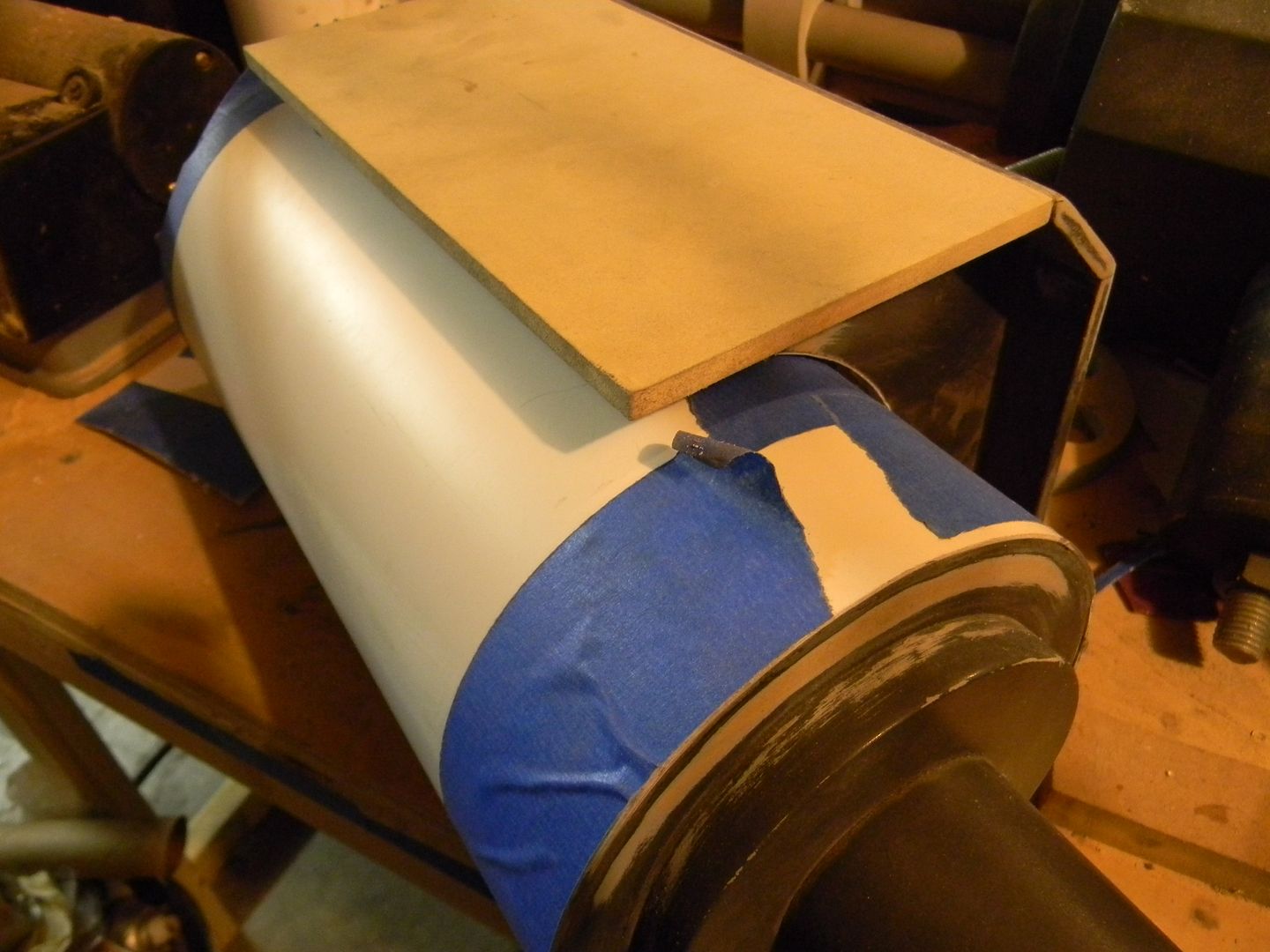
The holes for the magazine well was much easier to measure and cut. After copying the other gun, I glued the salvage magwell on top of the new skin and cut out the hole.
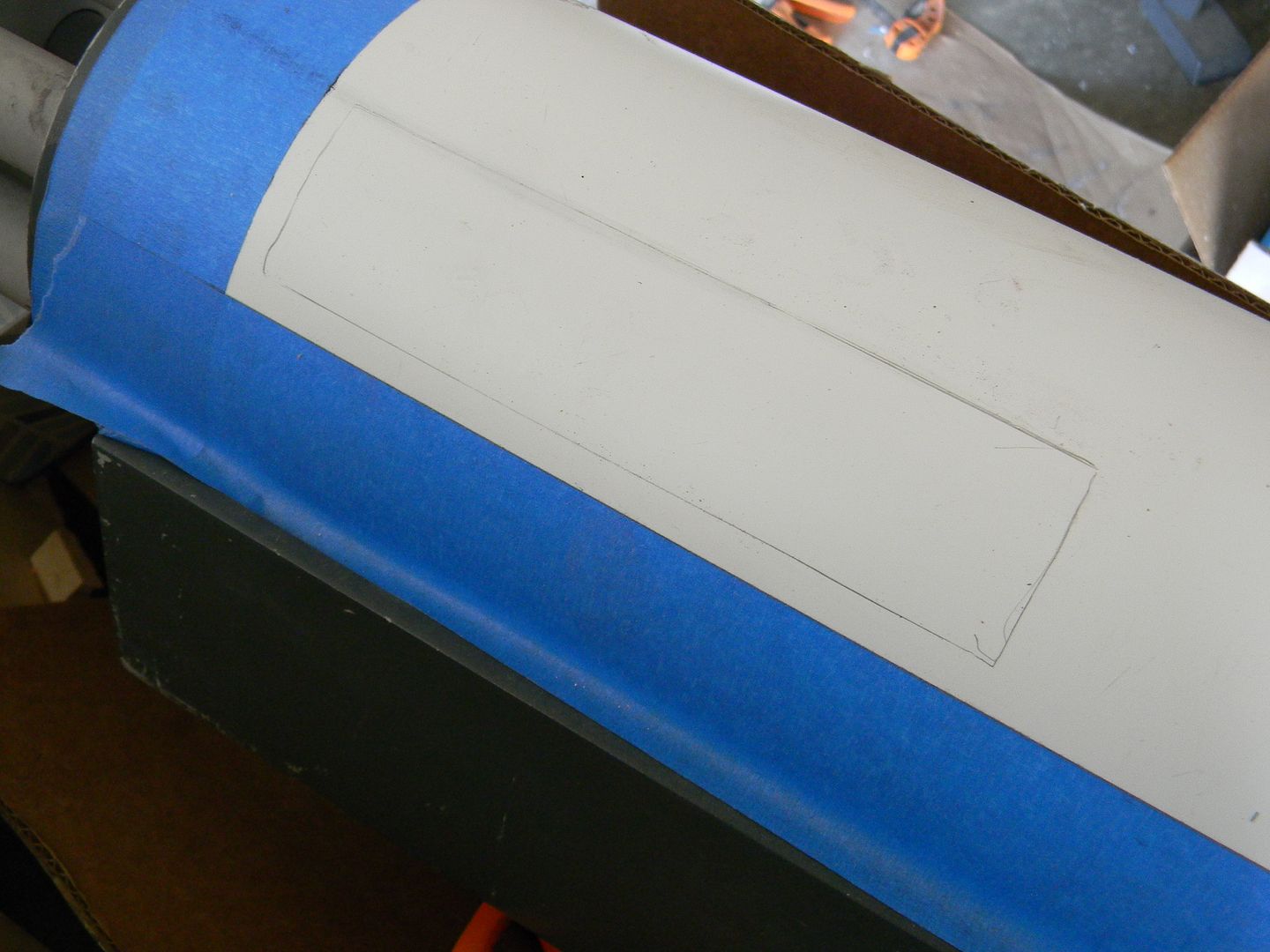
Welcome home, you 8 year old piece of MDF.
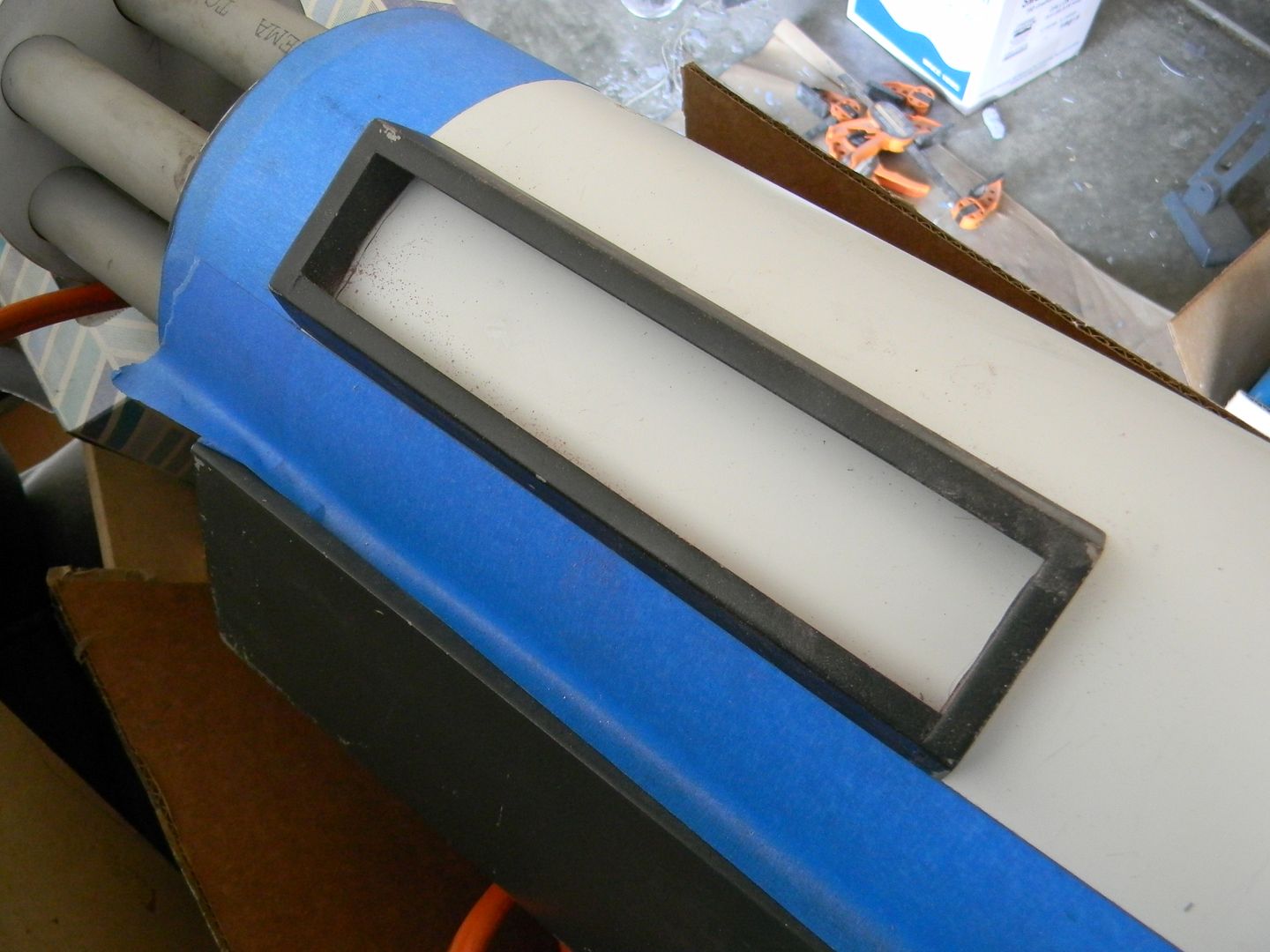
I once again had non-distorted miniguns! The other side needed moderate filling and sanding to preserve.
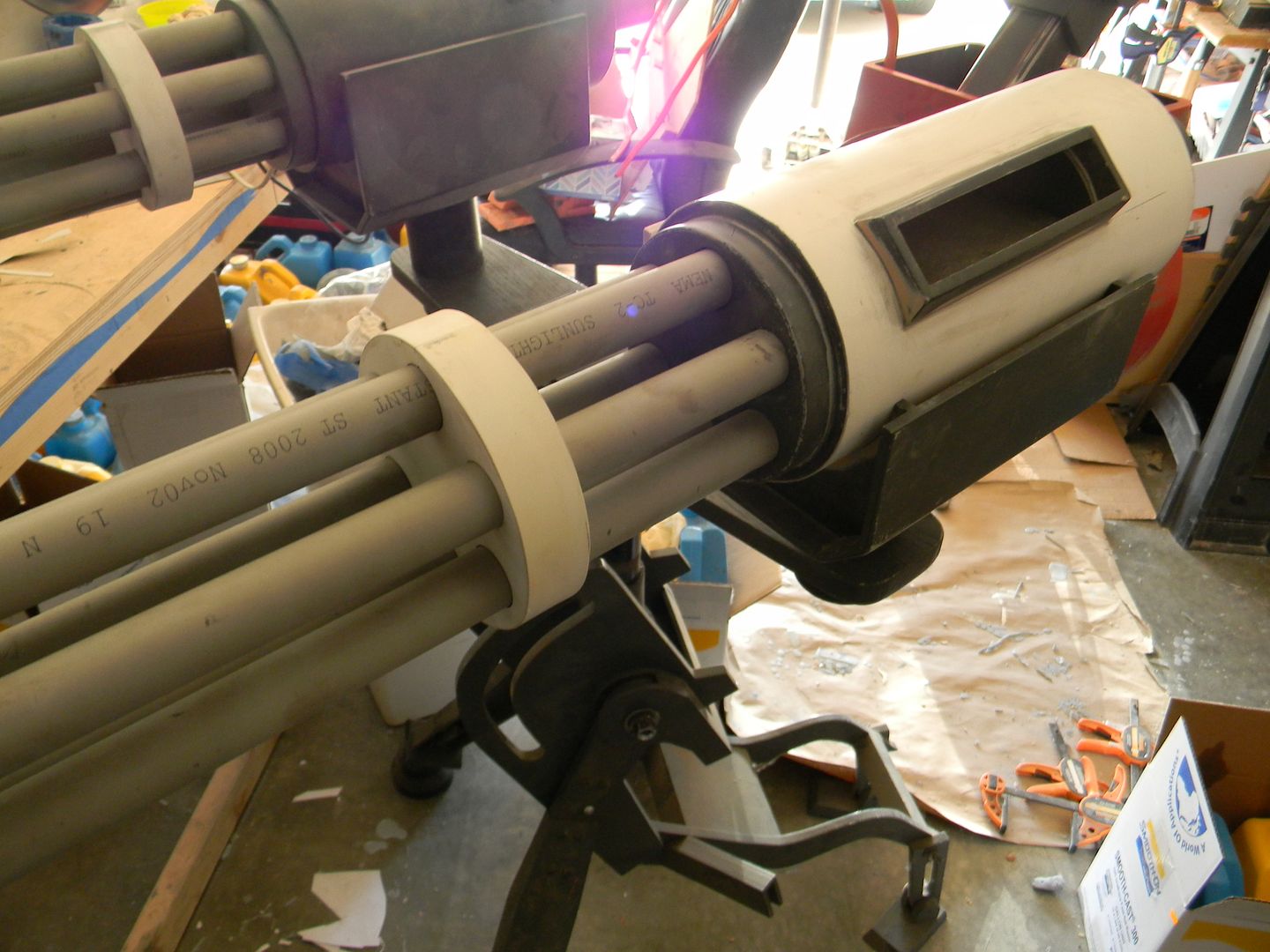
I skimped on photos for the rear most legs. Surprised? Anyways, this was kind of a pain. I didnt want to just use a plate or a saucer. The feet in game have a very angled but subtle look to them. I cut one out on a scroll saw, adjusted it as needed, and made a bunch of copies. I did some half-assed math to do this, but more than anything I'm pretty sure I just got lucky that it all fit together. The inside circle doesn't matter since its getting cut out for a PVC coupling.
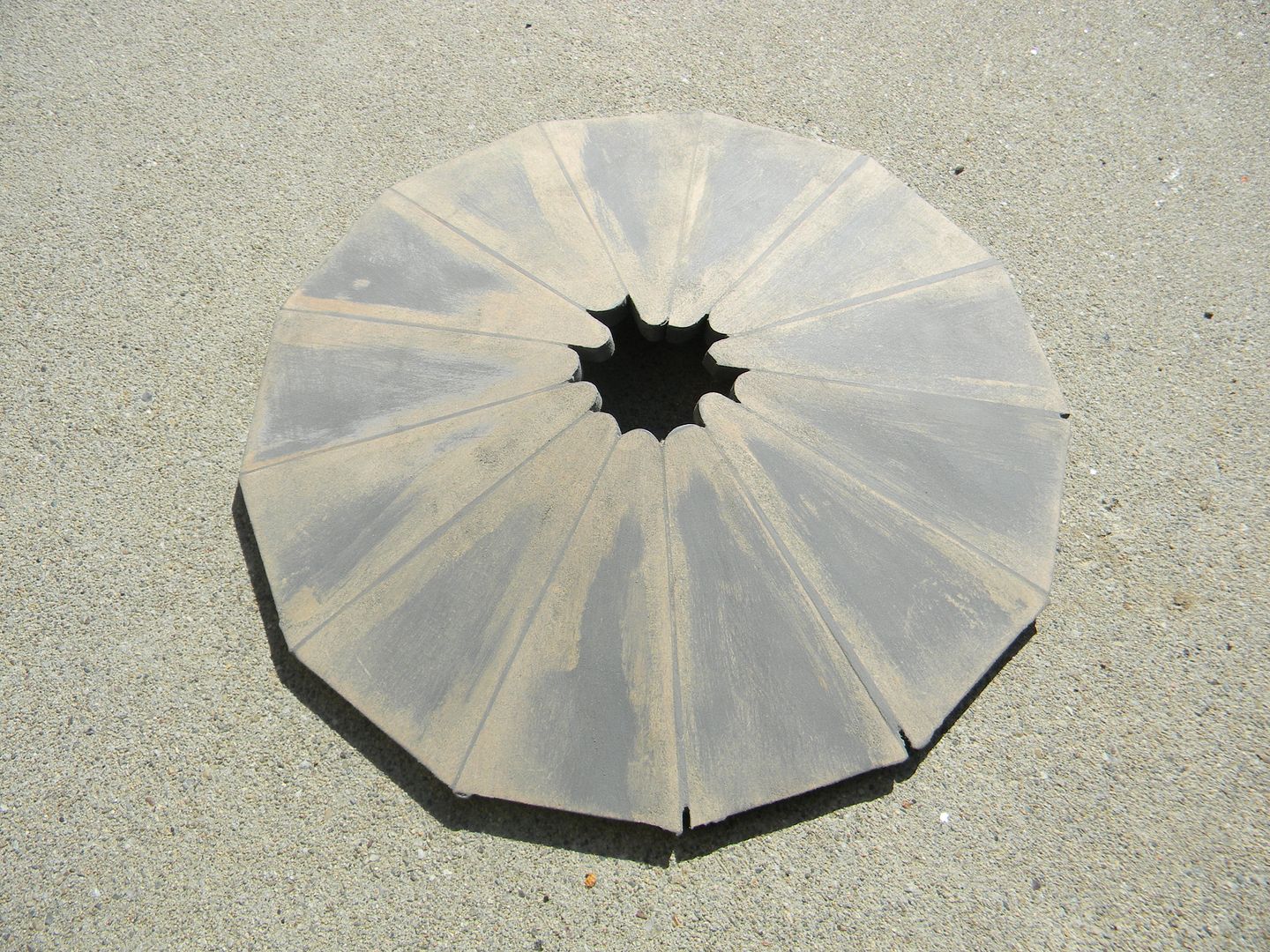
New guns mounted, new feet taking shape.
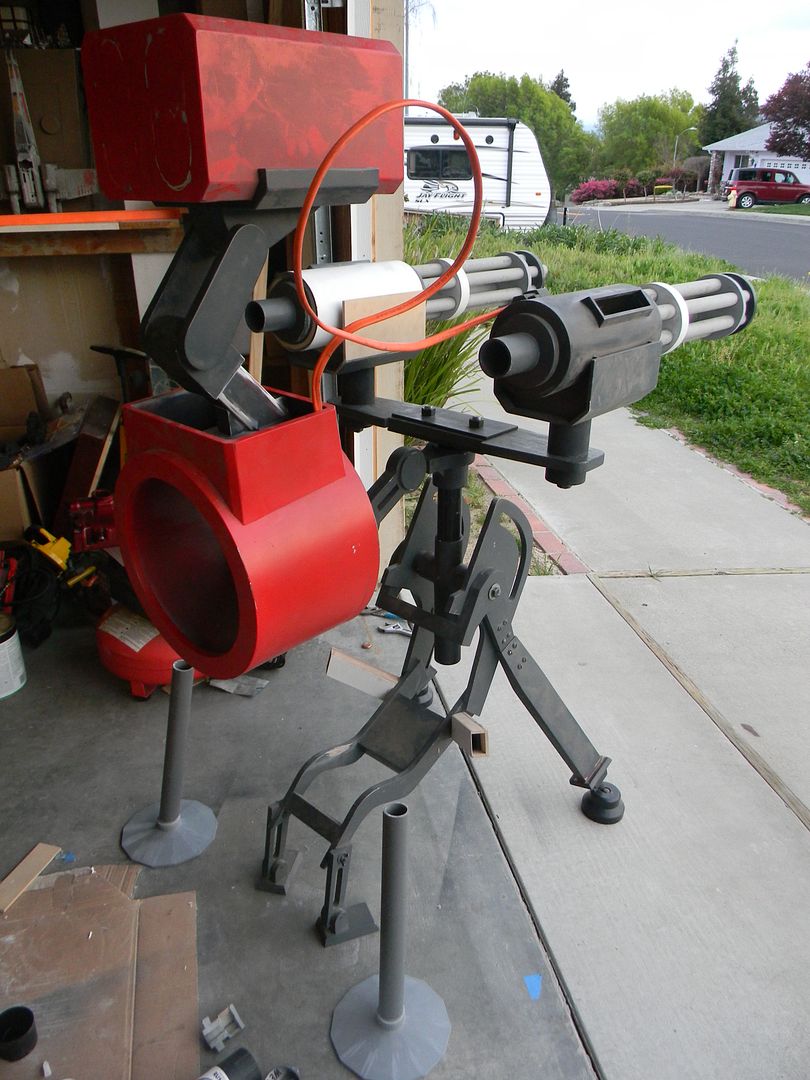
These rear legs....were a complete pain. No amount of screenshots could give me the correct angles at which they meet. They are kinked on at least 3 axis' and nothing is perfectly horizontal or vertical to reference off of. It took a lot of temporary gluing and real world fitting/frustration to get these right.
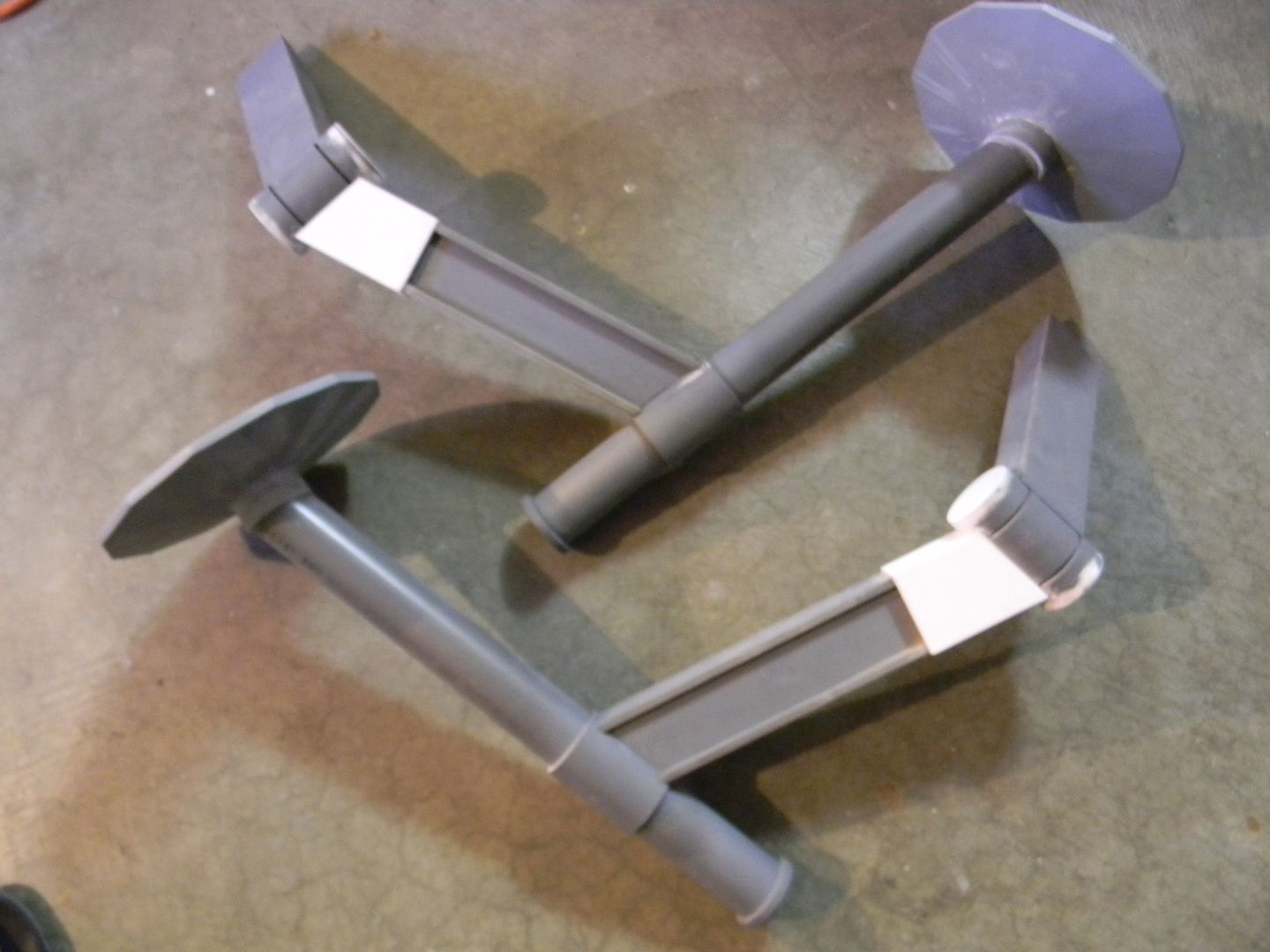
Time to paint (Again) and make some ammo belts! Before I forget, Those rings on the barrel are made from 1/2 inch MDF. Except for the white ones, which are styrene to keep the weight down. 21 year old me didn't own a hand drill, and certainly not a drill press. They were ALL drafted by hand and cut by hand on a scroll saw. It was a ton of work. The styrene holes were sanded out with a dremel.
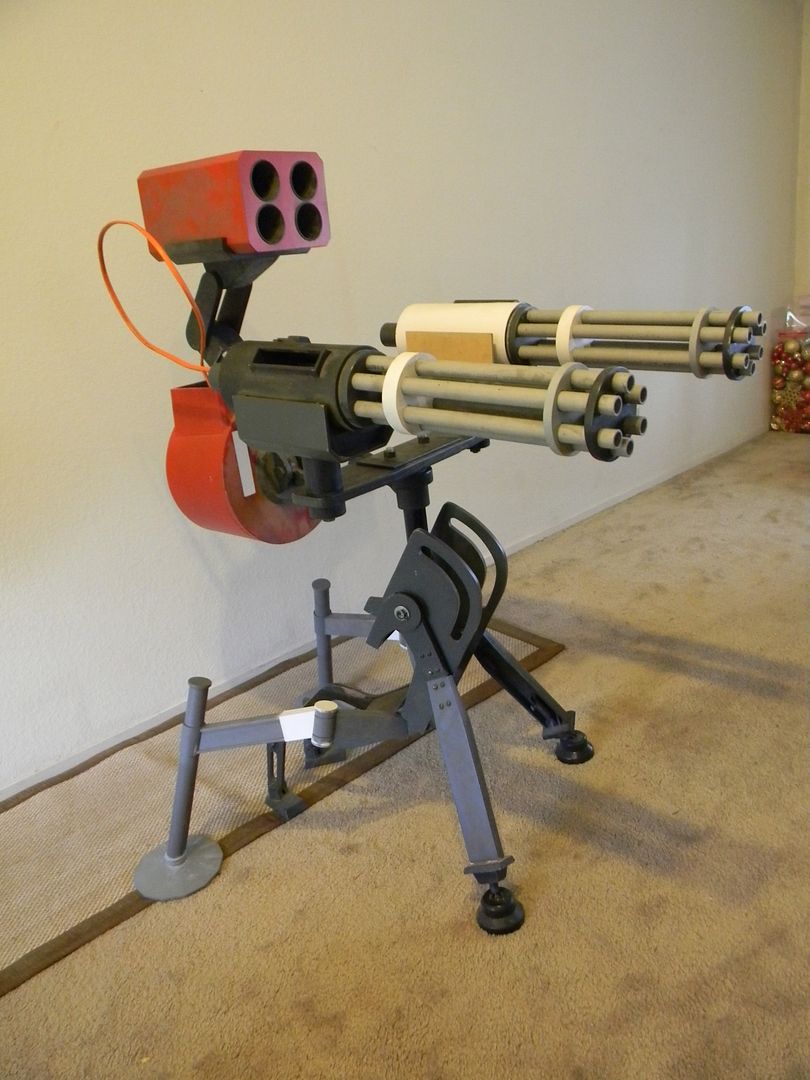
Not only was the old paint showing its age, but the company that make the paint doesn't offer it any more so the new parts wouldn't have matched. It all got sanded, primed, and painted. Again. Which is a few days of work by itself.
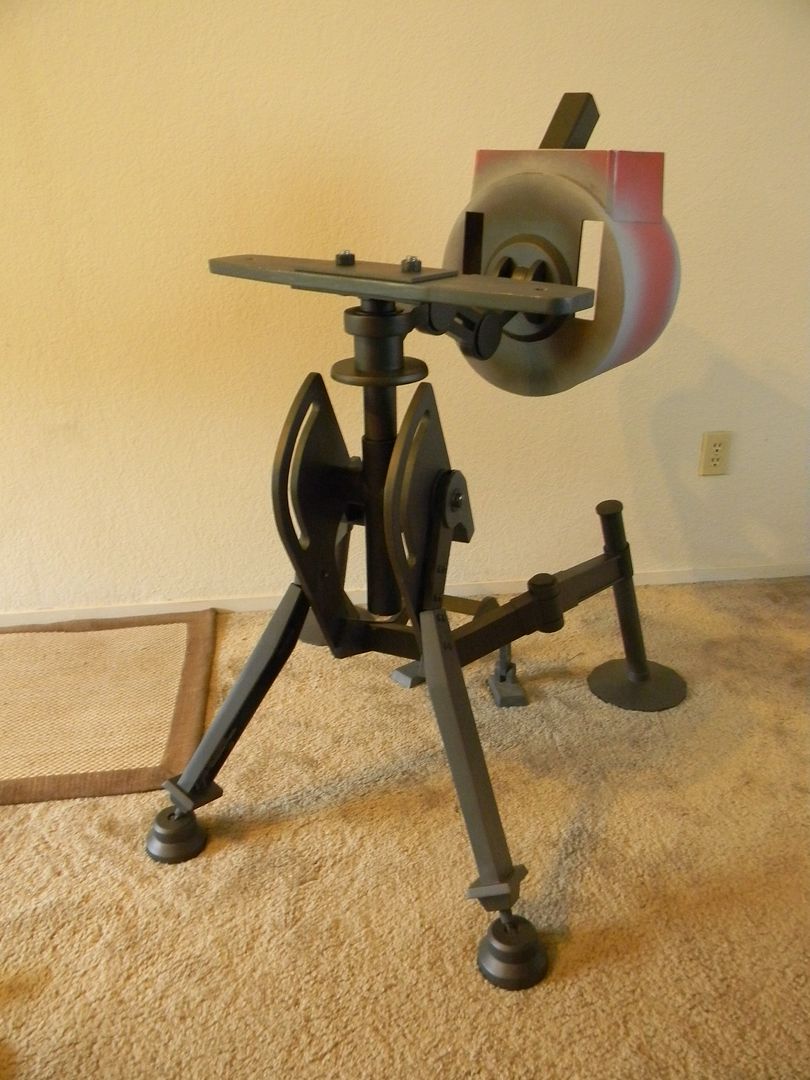
The ammo belts were hastily made from EVA foam, and were the only rushed part of this build. I wanted to get it ready for a local convention, called Silicon Valley Comic Con. Do I need to mention for the Nth time that I didn't take pictures?
The results are nothing short of spectacular. Not only is this fun to have at a convention, but this bad boy greets guests in my living room. Every day. So worth it.
Photo by Asian Treehouse Studios.
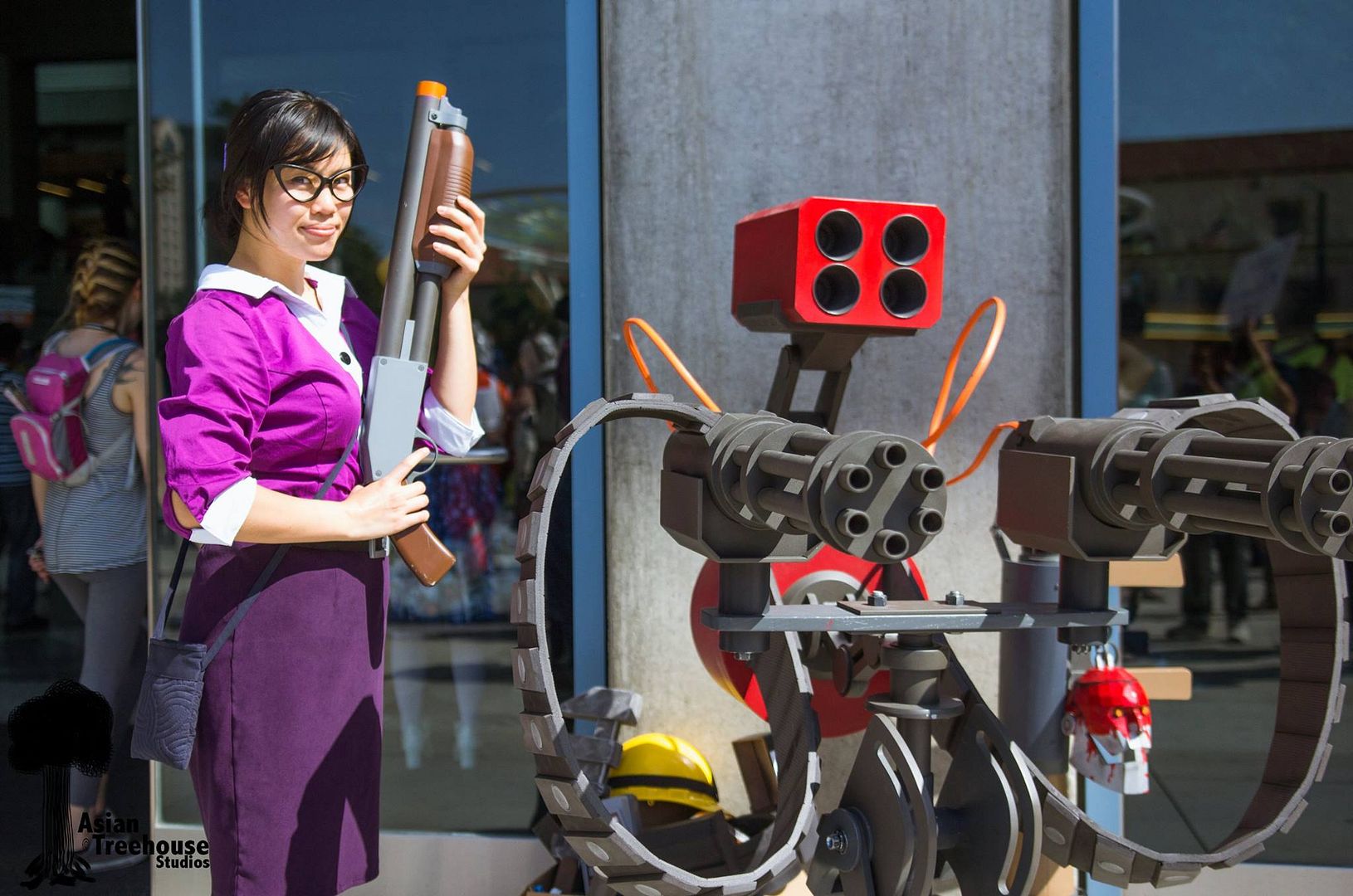
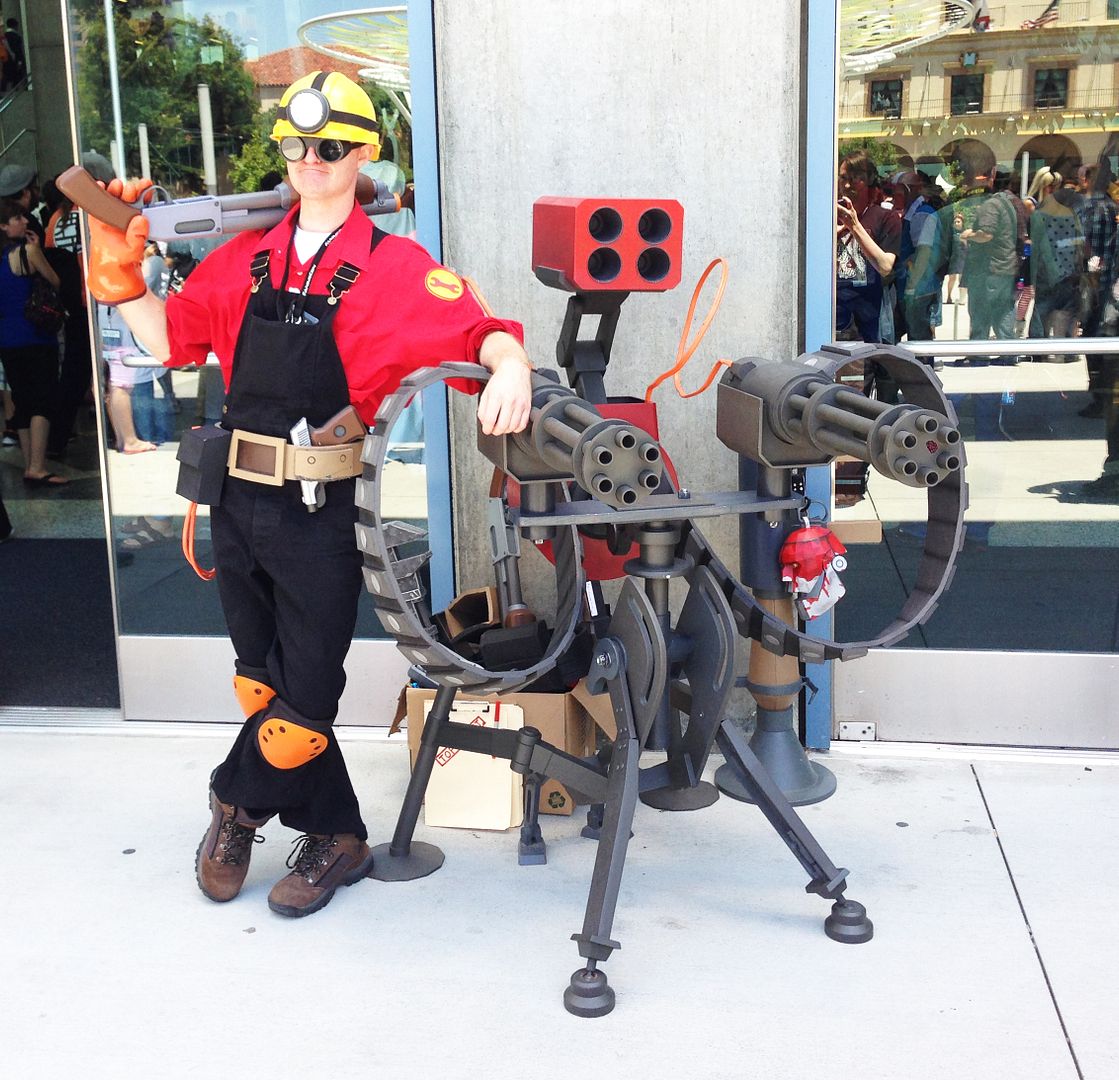
Photo by Neeko Cosplay Photography
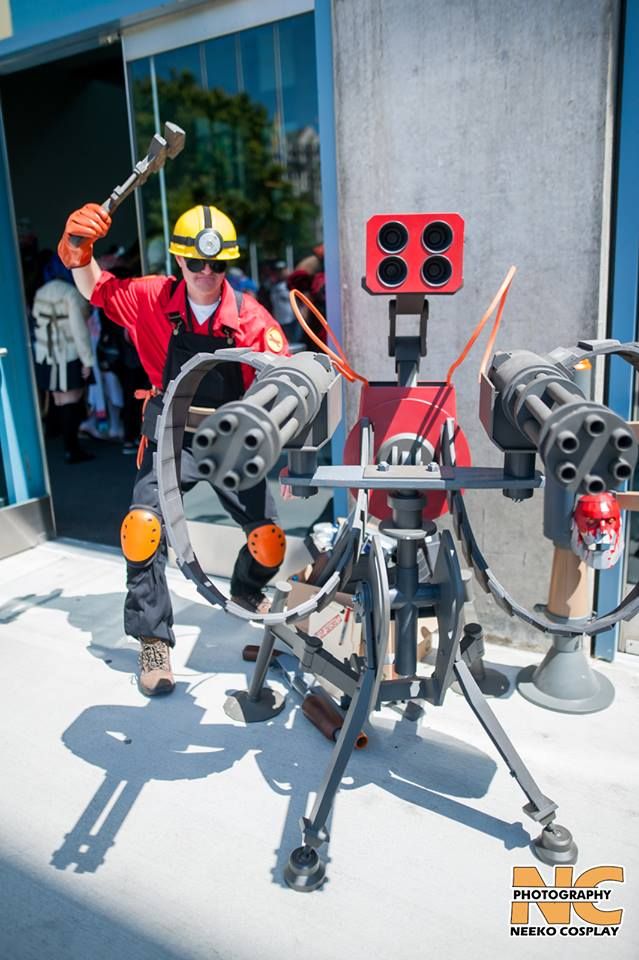
Photo by Kiel of Kairu Photography
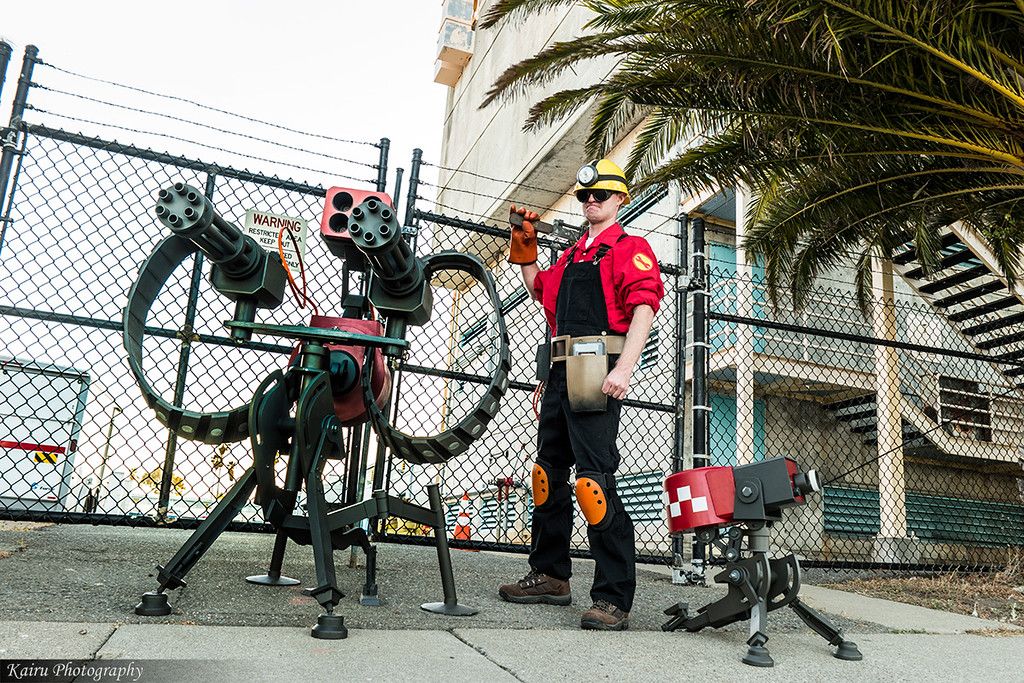
I entered a costume contest for my first time. I wore my soldier costume instead of my engineer, and brought the sentry....
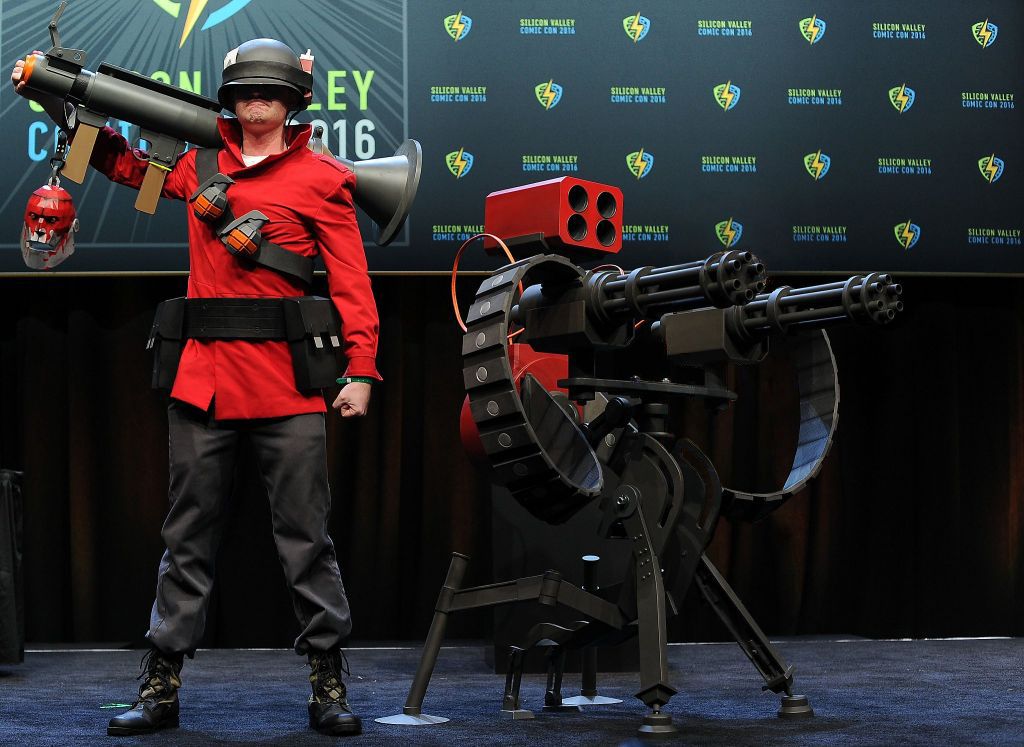
The result was my first award! hooray!

Yeah, I don't think I can top that, but this isn't the end of my sentry gun builds...