Every command center needs at least 6 of these....So, I set out....to make at least 6!
Reference image from some....random...source.
Reference image from some....random...source.

I started out in digital and used the StarCraft 2 Map editor to drop some SCVs at various angles around a command center model. I accounted for distortion and dropped it into a photoshop file, using rulers to make my measurements and scale relative to the command center I was already building.
I started with the intakes above the engines.
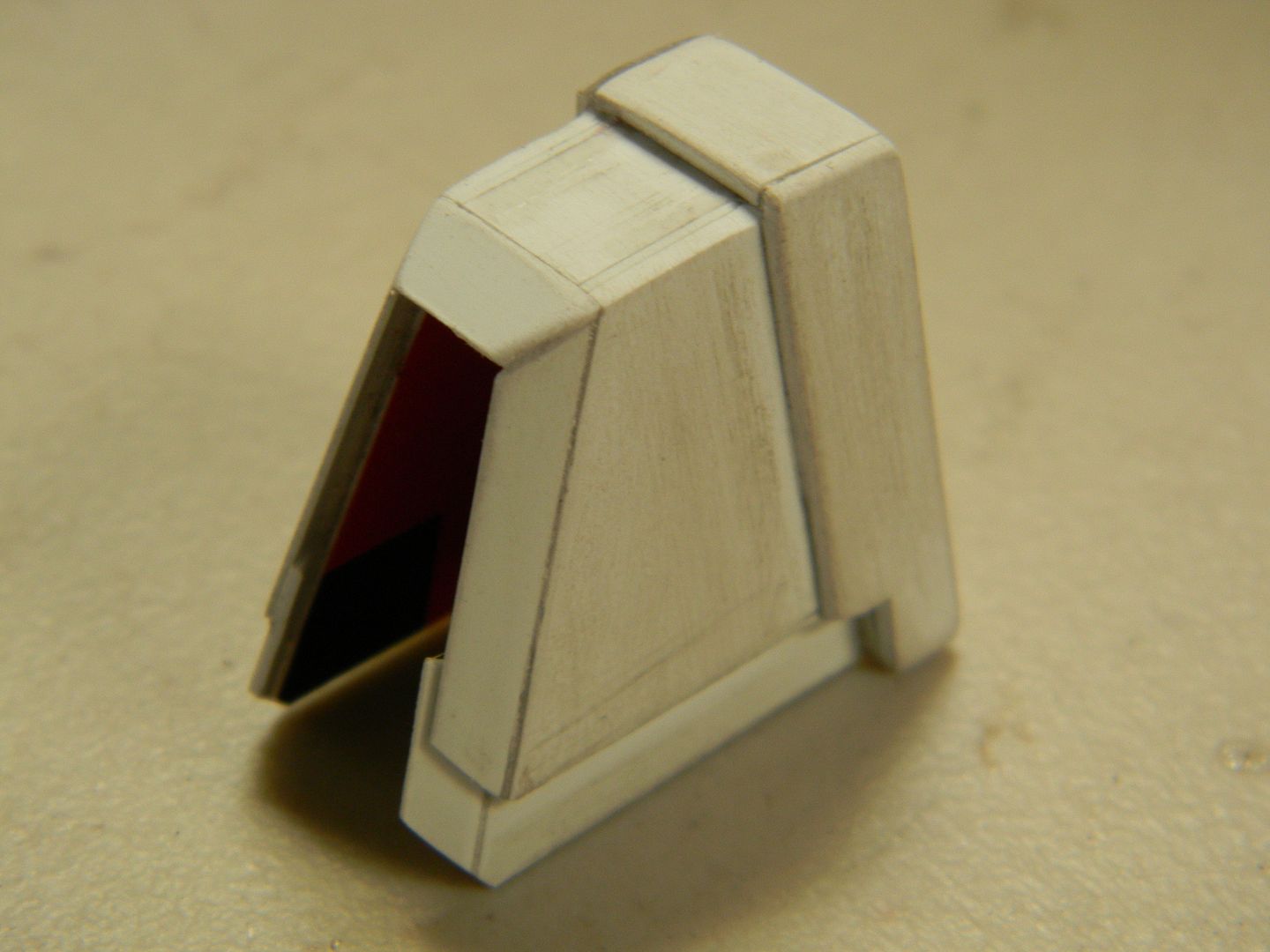
I carefully cut out some tiny strips and inset them as grills. I also began drafting and cutting paneling for the legs/feet.
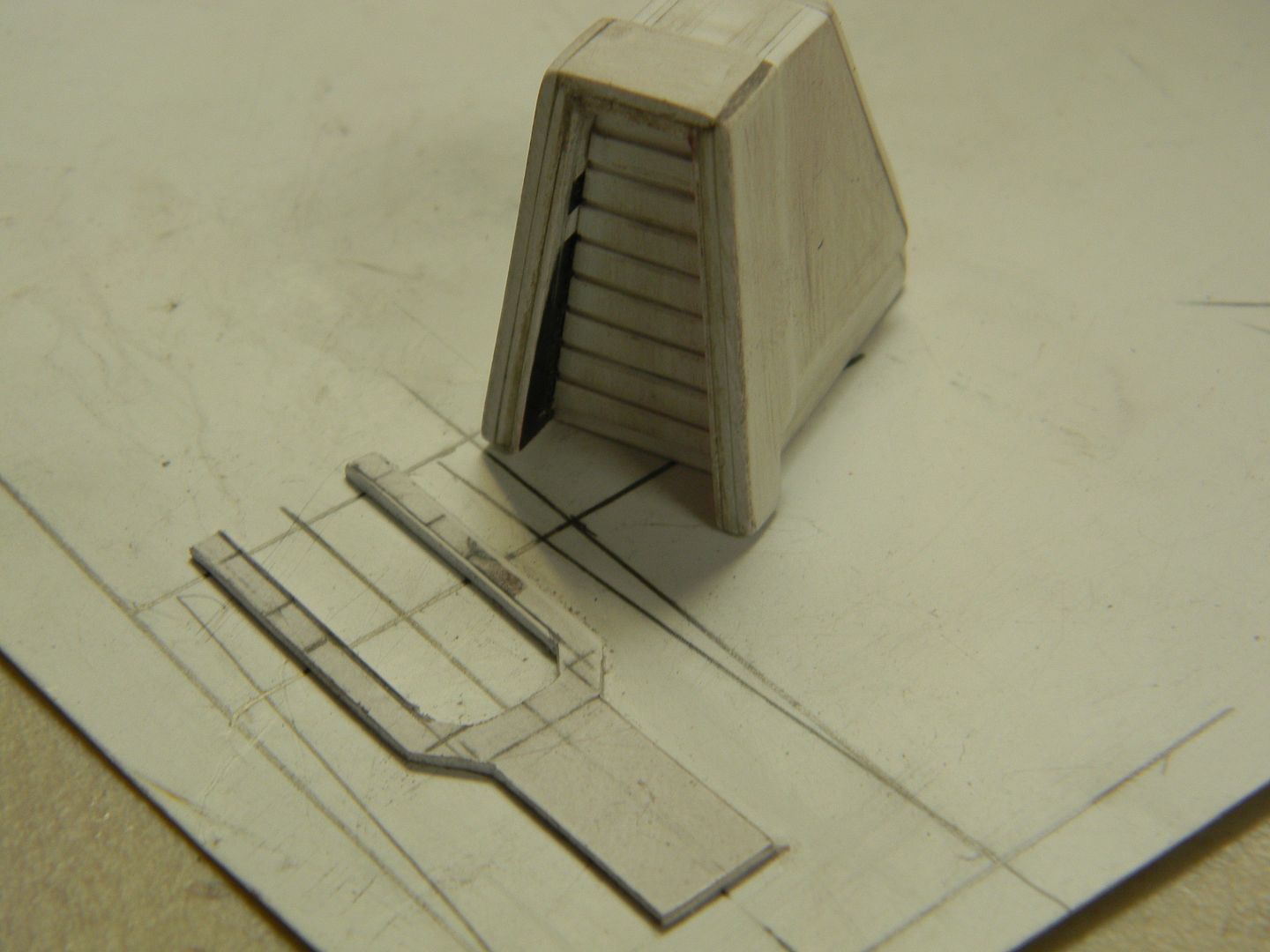
The feet were completed by simply taking my time and layering up styrene, bit by bit, edge to edge.
The panels in front of the engines were made by adding styrene atop a 1/8th inch piece of beveled MDF. I had these three parts done fairly quickly!

The "claw" was made from beveled MDF as well, with styrene between layers to produce a panel line look.

I glued down some teeny styrene bits to this MDF part before cutting out the general shape of the forearm.
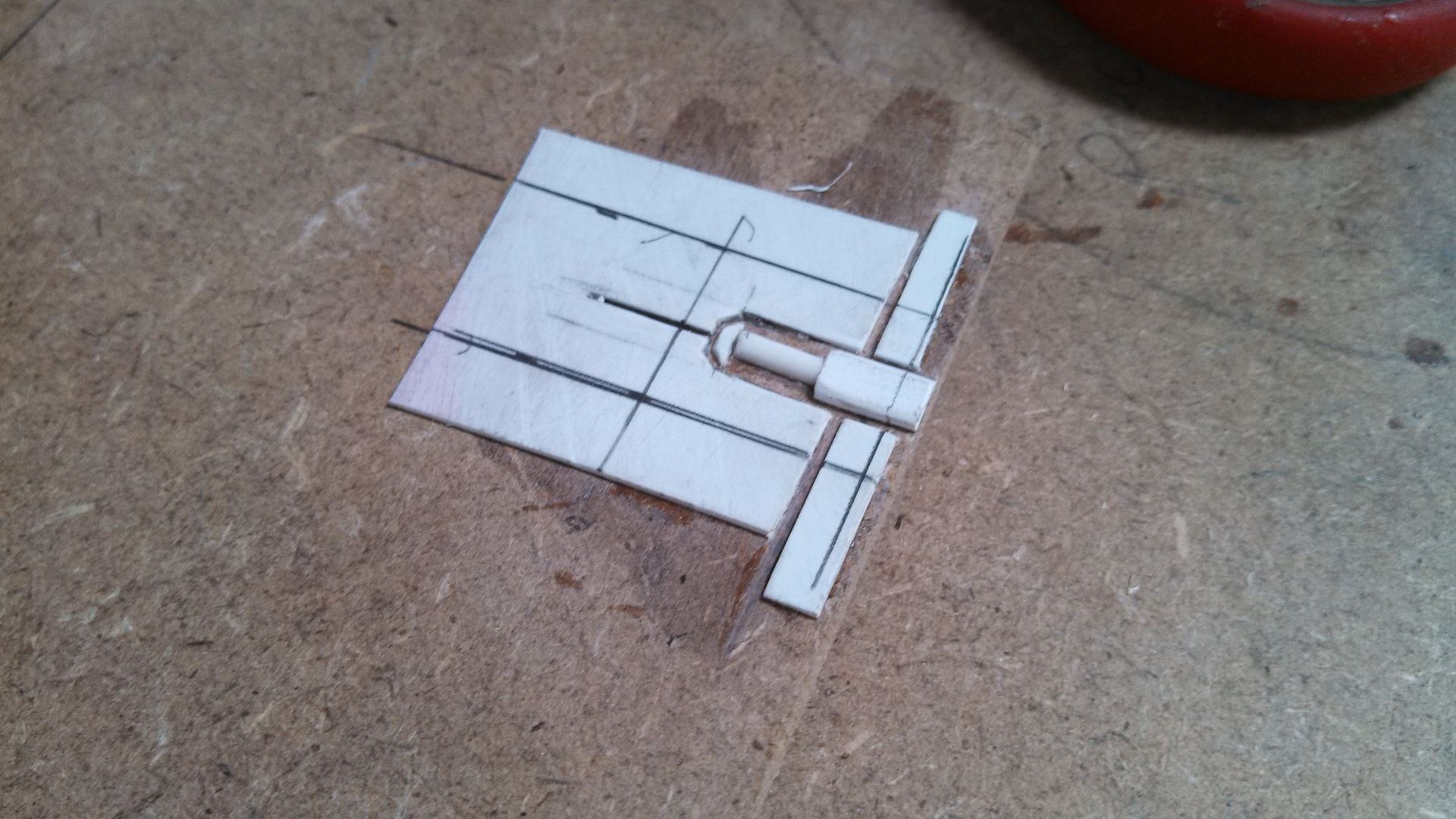
I had to to this twice, as well as make the side panels.
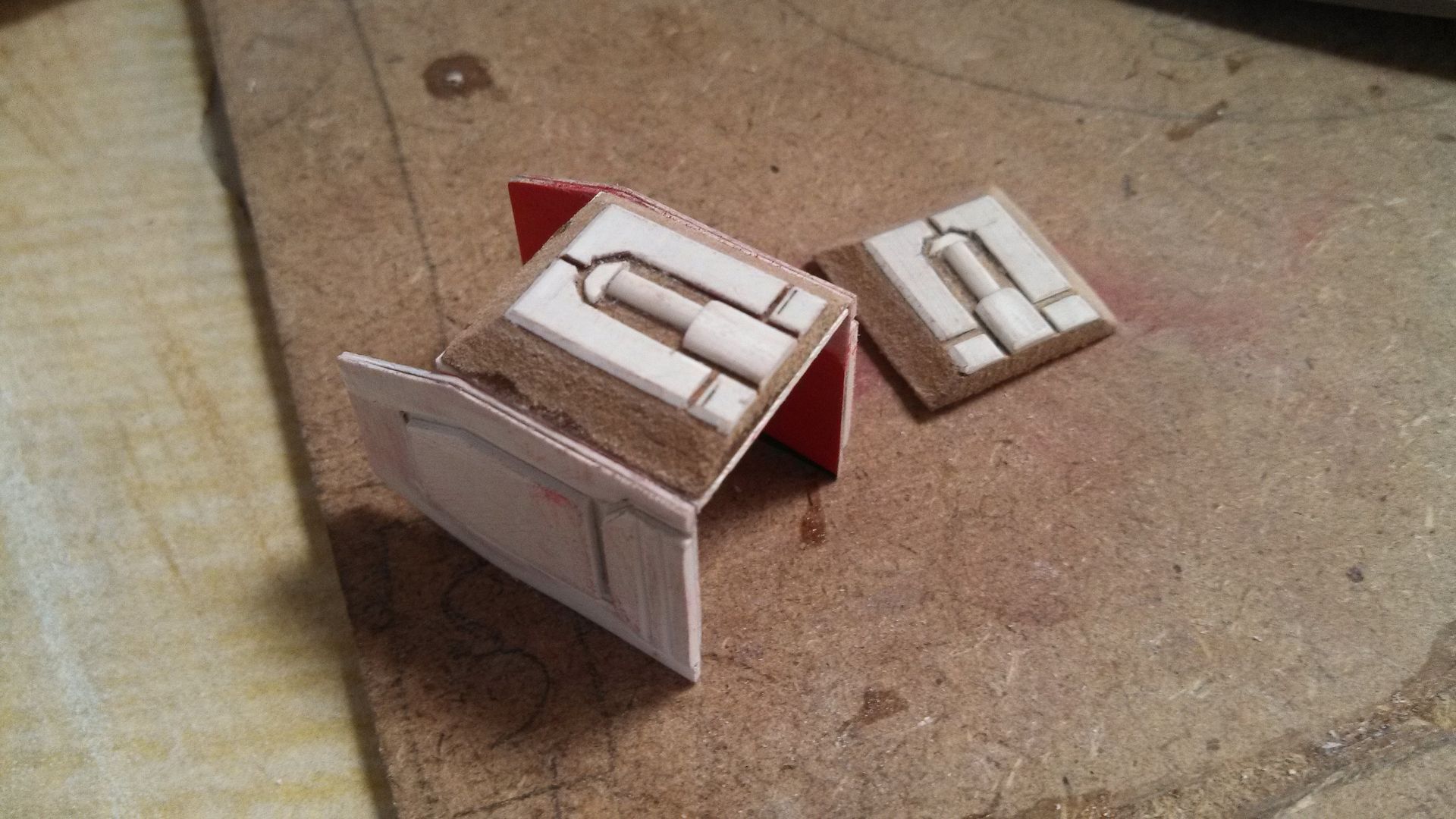
I used more or less the same techniques to build the cockpit and upper arm.
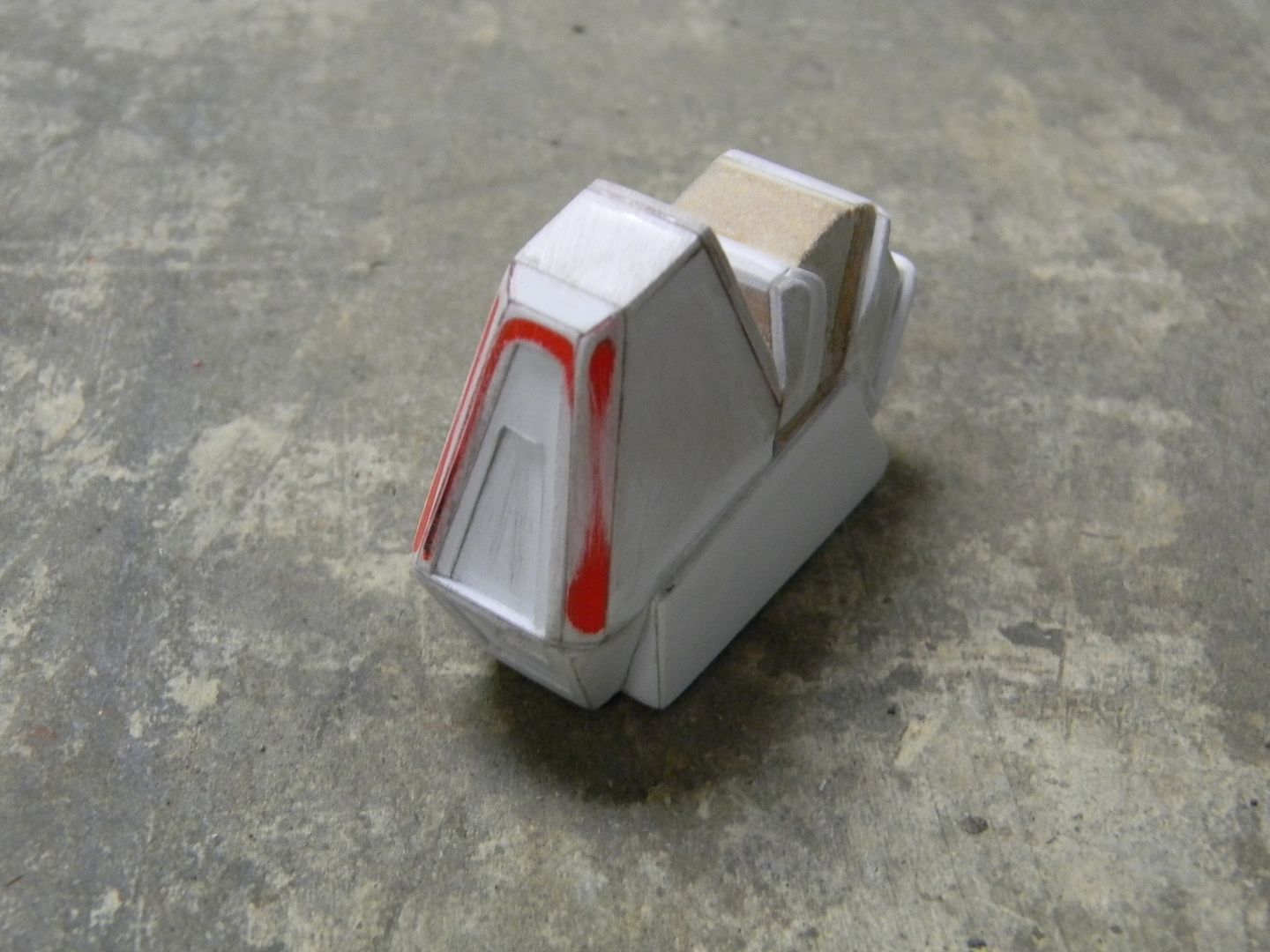
Here are the parts so far, primed and sanded. I don't have progress pictures of the drill, but the spiral part is simply half round styrene that I got warm and bent it around a wooden cone my friend turned on his lathe.
I cast up some engine intake copies, and added a lip around them to make them specific to their respective sides, rather than sculpt them both individually.

Then I cast the rest of the parts, which made other parts easier to size and make assemblies of, to be cast again.
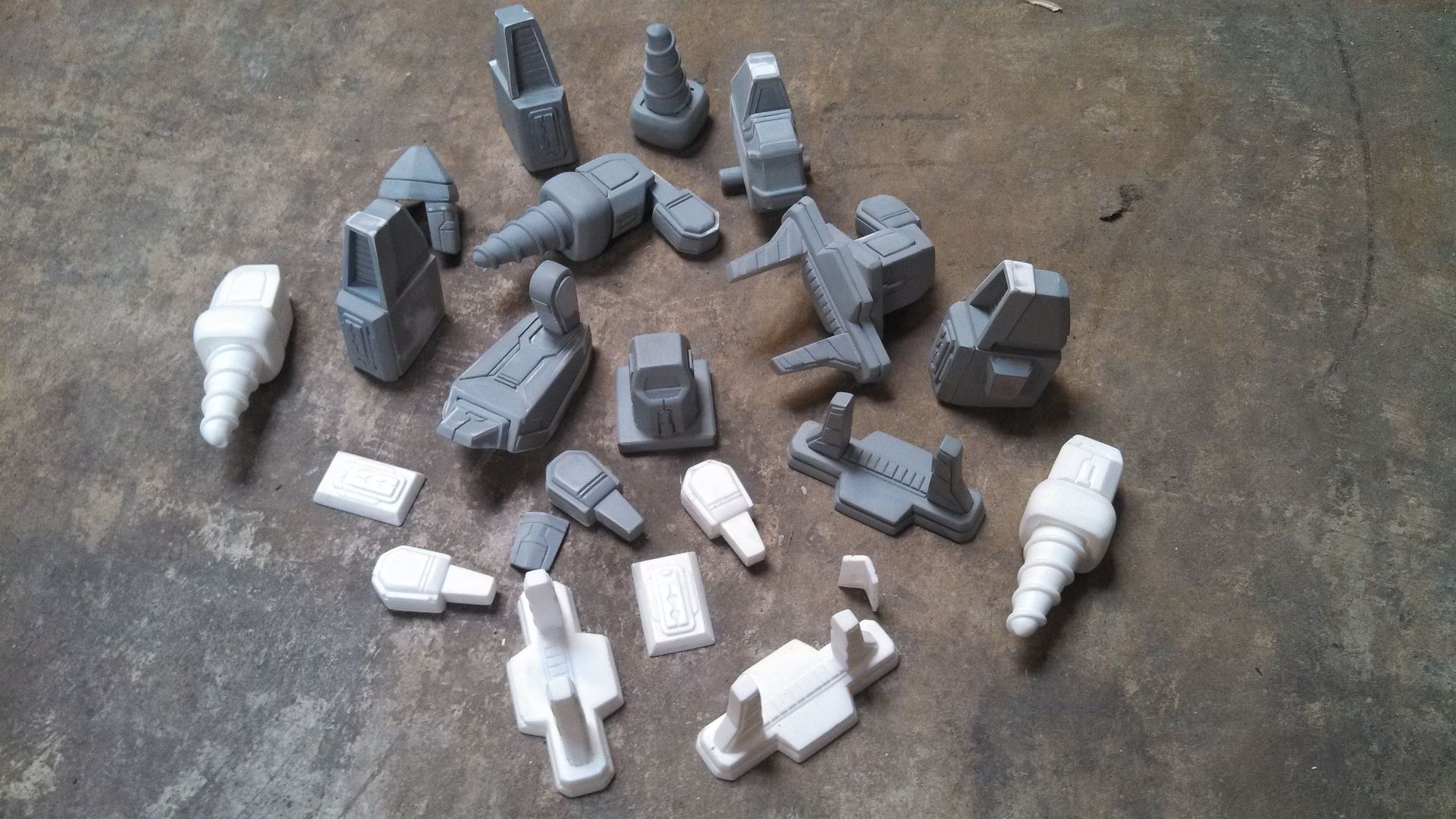
Before everything went together, the exhaust had to be made and cast. The cone was shaped by cutting out a hexagon, and then planing down the angles on a belt sander.

The exhaust fin is three layers of styrene, cut down the middle, then re-glued at an angle and sanded smooth.
They got cast, and the centers got bored out for future lighting attempts. Those fins are a real pain to cast!
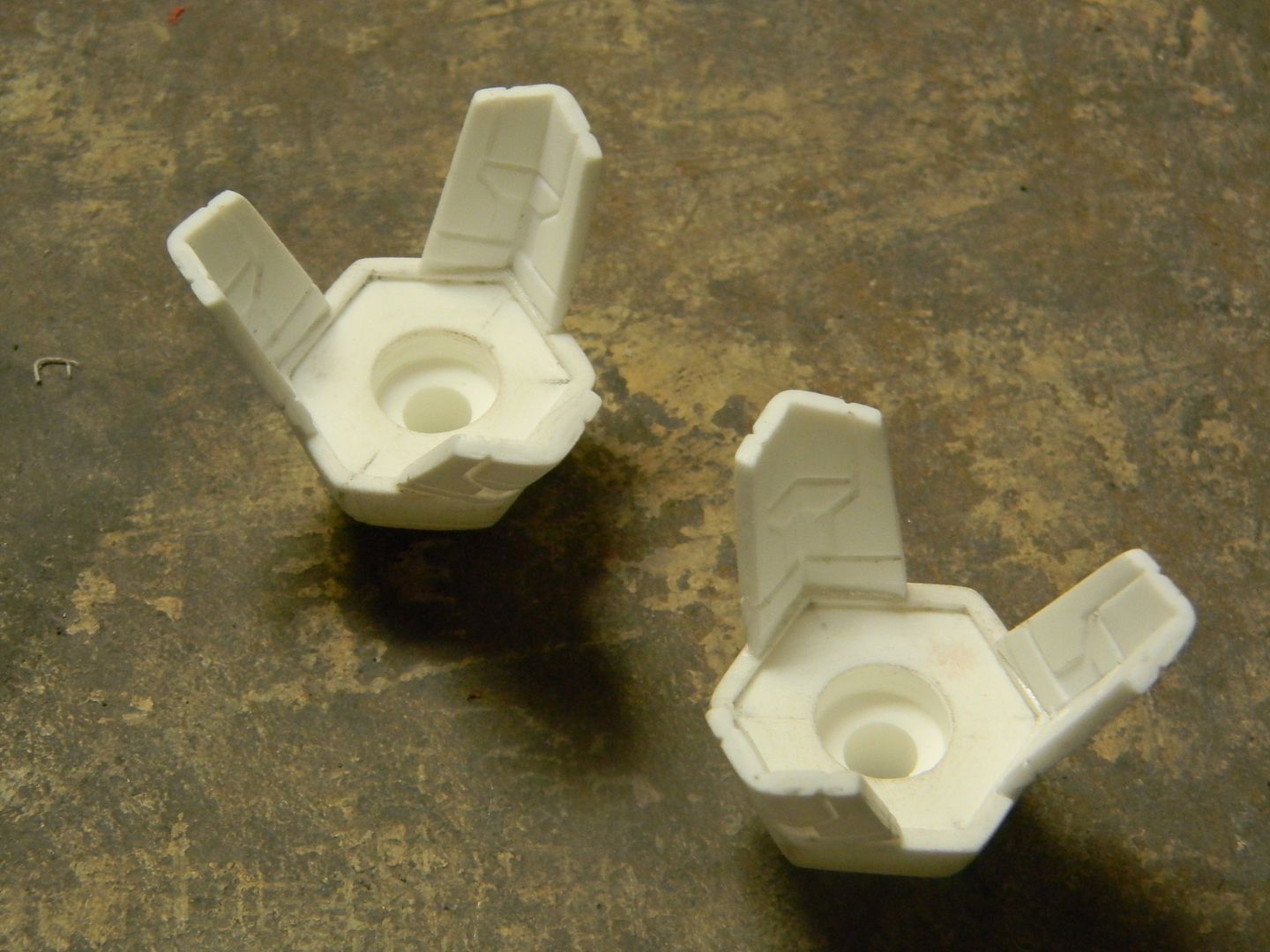
With all of that prototyping out of the way, I could start trading in my minerals for more SCVs....
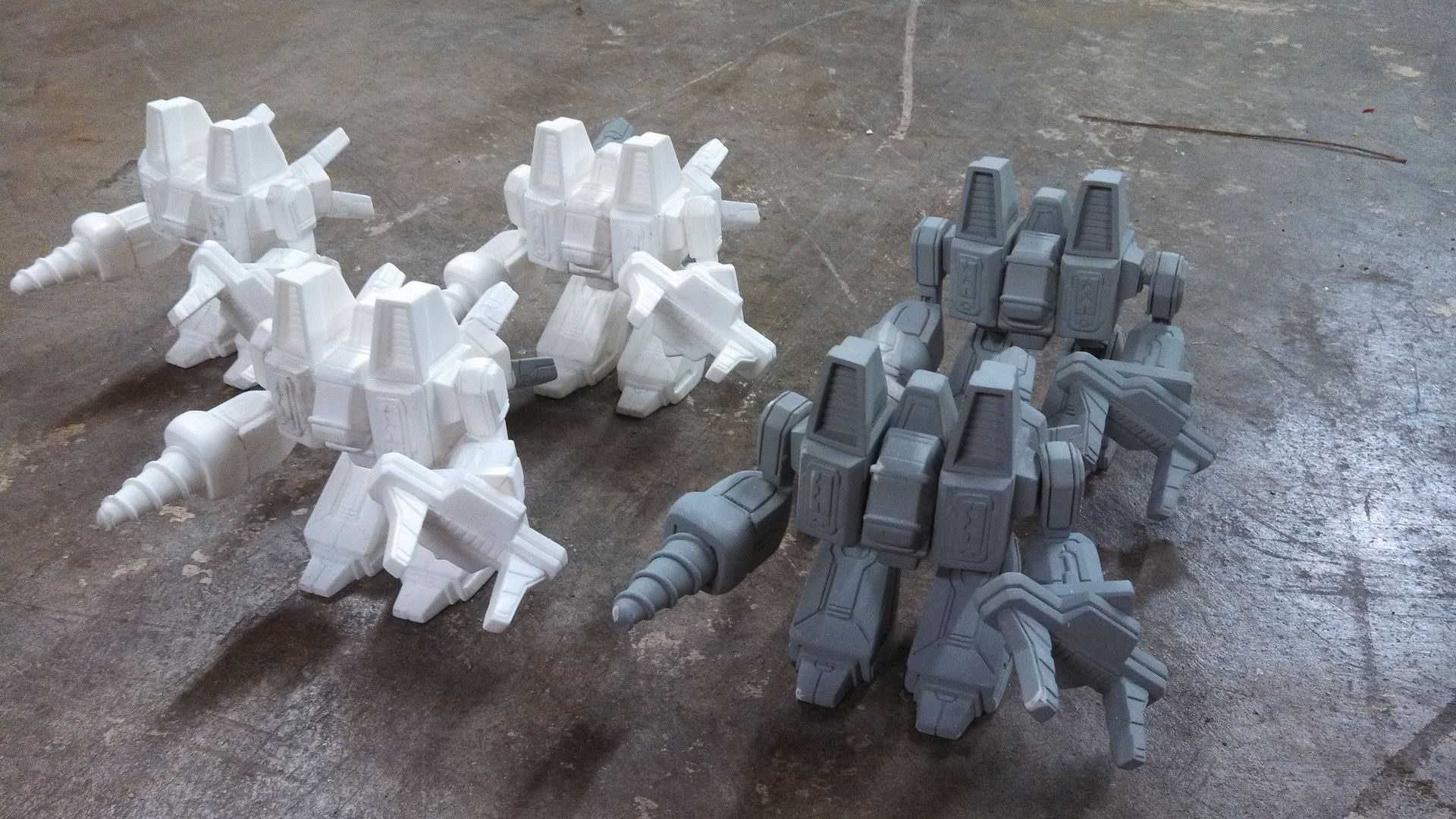
One of the casts got special treatment, and received some ABS/PVC joints out of some old Gundam action figures.

The base color is "colonial red" which is more of a red with a hint of grey, and looks more serious than most reds out of a spray can.
Theres quite a bit of grey variance going on here, and the cockpit was painted metallic like the game with some pre-shading and light weathering all around.

The claw and mid-section is probably the most fun to paint up.
Lastly again, the exhaust tips.
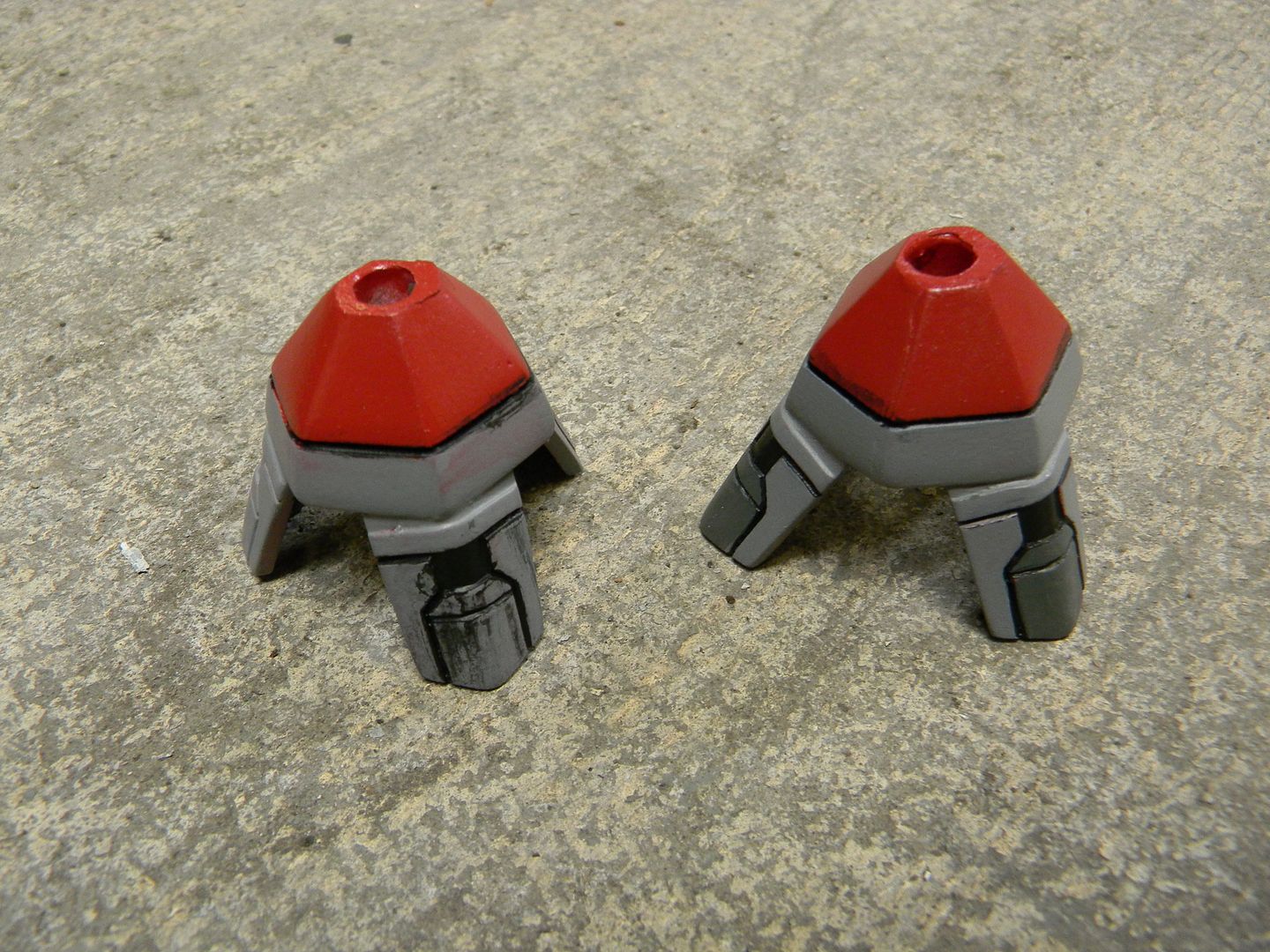
All done! expect more of these and a photoshoot down the road.
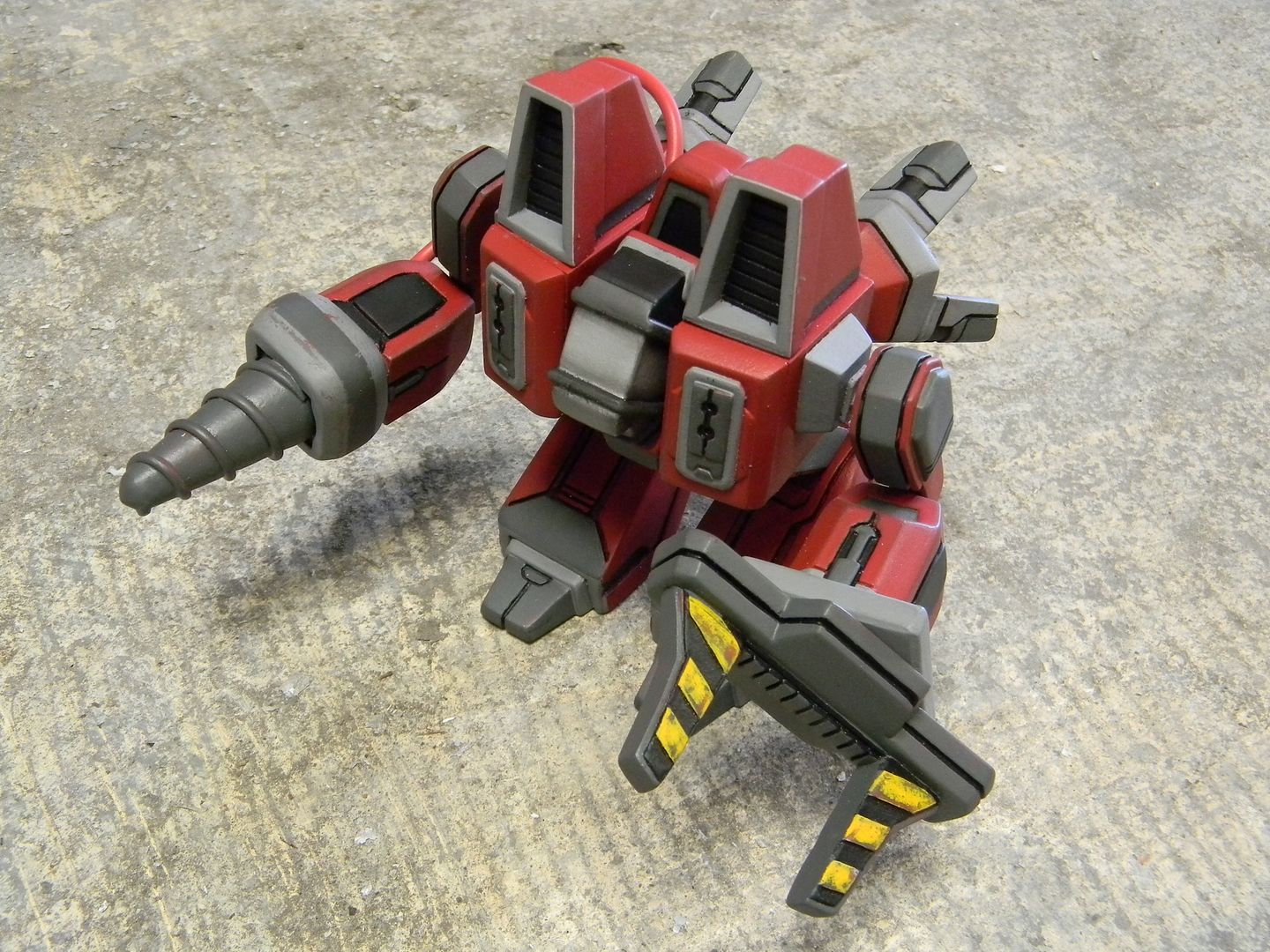