I did a really lose fit to see how much room I had to play with.
If you look closely, you can see that this part has some really large corners sticking out. In the game model, they "clip" into the models of the individual feet. Instead of attempting the giant headache of how the corner of a rectangular prism (with a draft angle on it) would intersect the bottom of the corner assembly + the knee joint at a 45 degree angle, I decided to completely avoid the issue all together and leave a small space between the parts. I'll just call it artist's discretion.
It got refined a bit into this, but I couldn't lob off the corners until I knew exactly how far the feet spaced.
The front and rear slivers of MDF were glued to the frame of the command center to help frame the center part. The center part is the part that is removable and holds the motherboard, etc.
Next it came time to tidy it up. These panels proved quite difficult to measure with all of the angles going on. On the bright side, the ramp keyed up perfectly!
The tiny little underside areas were carefully filled with sheet styrene. This is near the thruster housing.
With the underside mostly sealed up, I could get back to some sub-assemblies. The thrusters are the defining part of the rear, so I wanted to get those done next.
Sort of like the feet, I went slice by slice, beveling and sanding before assembly. I did the main thruster first.
The lines were done with just an exacto and the folded edge of sandpaper.
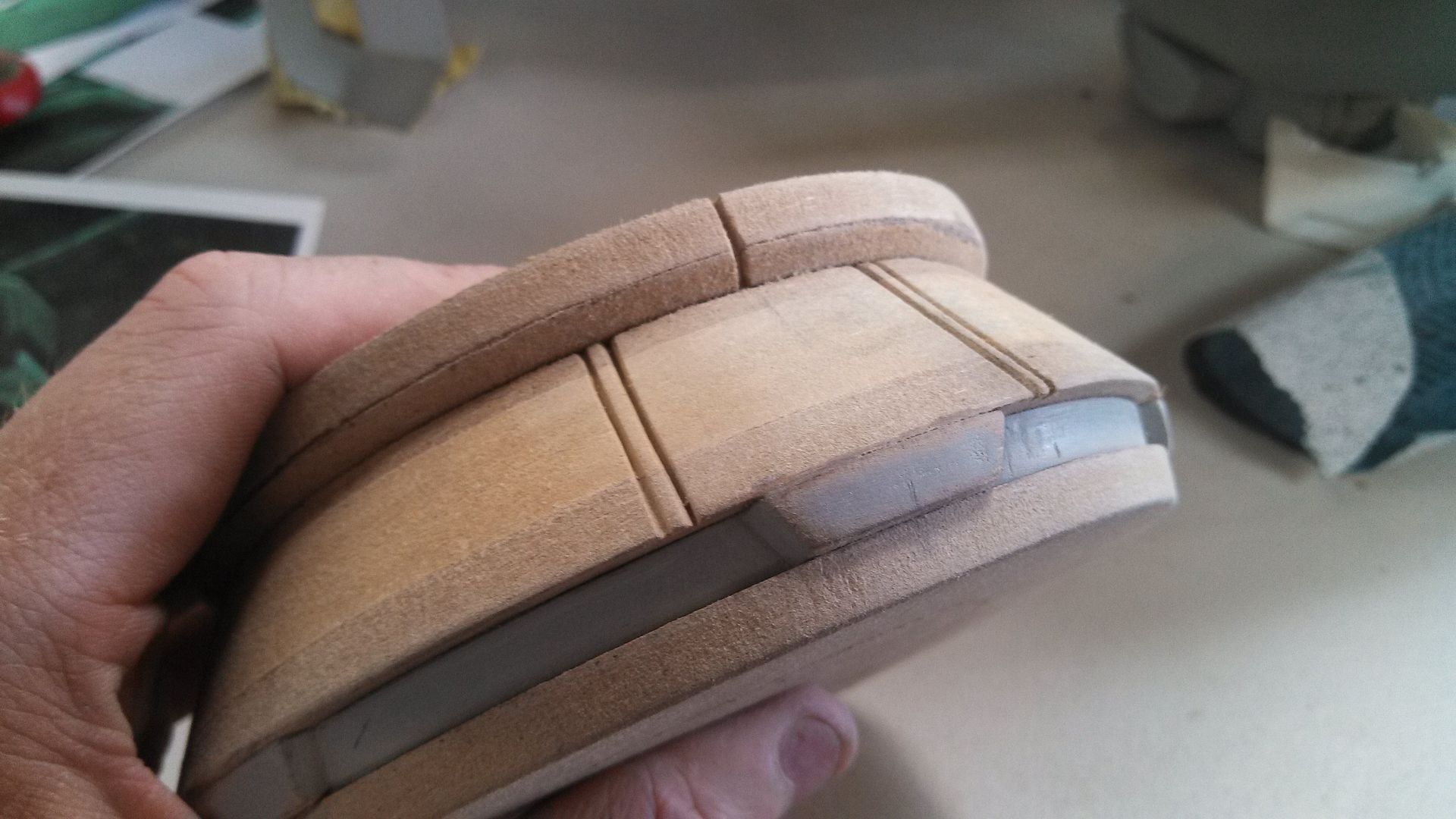
Some more progress on the housing, as well as trying out the new thruster! looks imposing. In game, the inside of the thruster tapers in and has some cool details, but since this is the port for the main exhaust fan, I did a straight cut to accommodate the largest amount of airflow possible.
The little guys were next.
Looks like cheesecake....
I used to use a drafting compass for this sort of thing, but realized a sheet metal one was much better as I could simply grind the line I wanted to cut. If I scribe it deep enough, it actually helps guide the scroll saw blade around the circle for a cleaner cut.
Cut and beveled.
Getting excited. Some bondo and filling the empty space should do the trick. There's so much chipping on the game model that I decided to avoid that entirely and thus made these stick out about .5"-.75" more than they should. Accuracy suffers a bit, but I avoided some huge headaches!
But, if you know me, then you should know that I hate Bondo. I use styrene to fill gaps instead. Its a bit tedious, but I absolutely hate sanding more than I need to, and this creates a much stronger bond between the parts than Bondo.
For the holes though, I have to take the plunge and get out the can, which brings me to the front. These little guys are some of the last cosmetic fabrication. I had to plane down the front panels first though.
The little brackets in the front were measured out before the sanding took place. This is just time management, I wanted the parts to bathe in primer while I did the sanding on the front. When you do this for a living, you'll be scrounging up ways to save time as often as possible!
since the corner assemblies are mirrored casts, it was only fitting that I mirrored these panels before finishing them off completely.
Measuring and getting the cuts this flush was work.
That's because every cut is beveled to some weird degree.
They were detailed with styrene, and slapped on there!
Getting close to done here. Time to cast the rest of the feet!
This pile was just begging to be put together. Its really rewarding seeing all of your casts come together for the first time, after hours of prep work. The thrusters were not cast, they were simply there for show.
Before Throwing everything together, there was some misc. detail here and there that needed attention.
The little slotted round parts above have a tiny blinking LED in them, so I needed room for that to show.
The detail on the right is cut out to have a small temperature screen that displays the general case temperature.
I think that's enough technical jargon, here's the result of all that hard work!
Scale insert sponsored by Coca-Cola.
Here's a couple shots of the innards. While being in the early stages, the rig is actually quite stable and not a whole lot of changes will be made for the final version. The first picture is the MDF frame before it went in the case. It looks like a headache, but its actually not that bad.
The motherboard sits at about 110 degrees vertical, as it is too tall!
Video here! (Might want to turn your sound down, sorry 'bout that!)